Corrosion-resistant mechanical arm and preparation method thereof
A corrosion-resistant, robotic arm technology, applied in the field of corrosion-resistant robotic arms and its preparation, can solve problems affecting the accuracy of instruction programs and other issues
- Summary
- Abstract
- Description
- Claims
- Application Information
AI Technical Summary
Problems solved by technology
Method used
Image
Examples
preparation example Construction
[0013] The invention provides a preparation method of a corrosion-resistant mechanical arm. The preparation method comprises:
[0014] 1) Mix ductile iron, silicon carbide particles, graphite fibers, manganese, nickel, chromium, ceria and vanadium pentoxide, and then conduct the first smelting to obtain molten iron M1;
[0015] 2) adding manganese trioxide, pentlandite, boron nitride, molybdenum sulfide, carbon black and niobium into the molten iron M1, followed by a second smelting to obtain the molten iron M2;
[0016] 3) Casting the molten iron M2 to obtain a parison, and performing heat treatment on the parison to obtain the corrosion-resistant mechanical arm.
[0017] In the above technical solution, the specific amount of each raw material used can be selected within a wide range, but in order to further improve the strength and anti-electromagnetic interference performance of the manufactured mechanical arm, preferably, in parts by weight, the The dosage ratio of ducti...
Embodiment 1
[0026] 1) After mixing ductile iron, silicon carbide particles, graphite fibers, manganese, nickel, chromium, ceria and vanadium pentoxide, smelting at 1700°C for 4 hours to obtain molten iron M1;
[0027] 2) Dimanganese trioxide (average particle size 20 μm), pentlandite (average particle size 25 μm), boron nitride (average particle size 30 μm), molybdenum sulfide (average particle size 20 μm), carbon black (the average particle size is 30 μm) and niobium are added to the molten iron M1, followed by smelting at 1500° C. for 2 hours to obtain the molten iron M2;
[0028] 3) Casting the molten iron M2 to obtain a parison (the temperature of the parison is 750°C), and keeping the parison at 800°C for 2 hours, then cooling down to 600°C at a rate of 10°C / min for 5 hours, The most direct water cooling after heat preservation is to obtain the corrosion-resistant mechanical arm, denoted as A1.
[0029] Wherein, in parts by weight, the ductile iron, silicon carbide particles, graphi...
Embodiment 2
[0031] 1) After mixing ductile iron, silicon carbide particles, graphite fibers, manganese, nickel, chromium, ceria and vanadium pentoxide, smelting at 1750°C for 3 hours to obtain molten iron M1;
[0032] 2) Dimanganese trioxide (average particle size 25 μm), pentlandite (average particle size 25 μm), boron nitride (average particle size 30 μm), molybdenum sulfide (average particle size 20 μm), carbon black (the average particle size is 30 μm) and niobium are added to the molten iron M1, followed by smelting at 1550° C. for 2 hours to obtain the molten iron M2;
[0033] 3) Cast the molten iron M2 to obtain a parison (the temperature of the parison is 800°C), and keep the parison at 850°C for 1 hour, then cool it down to 500-600°C at a rate of 15°C / min and keep it warm 3-5h, the most direct water cooling after heat preservation, that is, the corrosion-resistant mechanical arm is produced, which is recorded as A2.
[0034] Wherein, in parts by weight, the ductile iron, silicon...
PUM
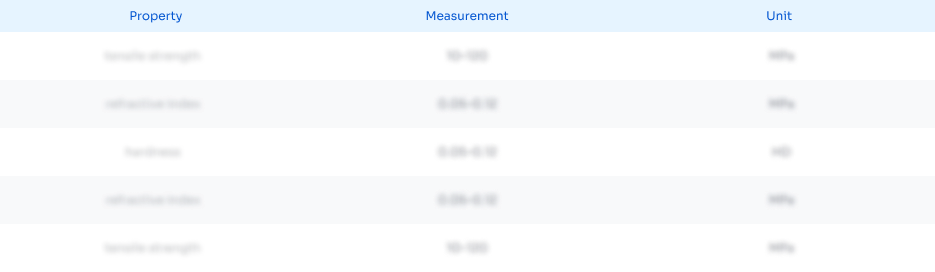
Abstract
Description
Claims
Application Information

- Generate Ideas
- Intellectual Property
- Life Sciences
- Materials
- Tech Scout
- Unparalleled Data Quality
- Higher Quality Content
- 60% Fewer Hallucinations
Browse by: Latest US Patents, China's latest patents, Technical Efficacy Thesaurus, Application Domain, Technology Topic, Popular Technical Reports.
© 2025 PatSnap. All rights reserved.Legal|Privacy policy|Modern Slavery Act Transparency Statement|Sitemap|About US| Contact US: help@patsnap.com