A method for preparing graphene-aluminum alloy composite material by electro-explosive spraying
A composite material and aluminum alloy technology, which is applied in the field of graphene-aluminum alloy composite materials prepared by electric explosion spraying, can solve the problems of poor wettability between graphene and matrix alloy, reduced graphene performance, and few graphene composite materials, etc., to achieve The effect of high product quality, reduced production cost and high production efficiency
- Summary
- Abstract
- Description
- Claims
- Application Information
AI Technical Summary
Problems solved by technology
Method used
Examples
Embodiment 1
[0028] (1) Sonicate flake graphite powder in HF solution with a solution concentration of 5% for 1 minute to remove impurities on the graphite surface, and finally rinse with deionized water to remove HF residual liquid. The purity is 99.9% at ambient pressure of 1000 Pa and 80°C. % of the graphite powder is dried under the protection of argon, and after removing impurities, it is dried under the protection of argon for later use;
[0029] (2) Put the graphite powder material into the ball mill, set the temperature of the ball mill to 60°C, and the grinding speed to 320rpm / min. After grinding, the finer solid product is graphite fine powder;
[0030] (3) The ultra-fine graphite powder is atomized with a high-pressure airflow, the nozzle pressure of the high-pressure airflow is 8MPa, and the outlet flow rate is 24.4m / s, and it is sprayed between the two preset electrodes. 20 A alternating current, the alternating electric field between the two electrodes has a voltage of 5KV, a...
Embodiment 2
[0033] (1) Sonicate pyrolytic graphite powder in HF solution with a solution concentration of 3.5% for 0.5 minutes to remove impurities on the surface of pyrolytic graphite, and finally rinse with deionized water to remove HF residual liquid. The pyrolysis graphite powder with a purity of 99.9% is dried under the protection of argon gas, and after removing impurities, it is dried under the protection of argon gas for use;
[0034] (2) Put the graphite powder material into the sand mill, set the temperature of the sand mill to 150°C, and the grinding speed to 350rpm / min. After grinding, a finer solid product is graphite fine powder;
[0035] (3) Atomize the ultra-fine graphite powder with a high-pressure airflow, the nozzle pressure of the high-pressure airflow is 9MPa, the outlet flow rate is 21m / s, and an alternating current of 10A is provided between the two electrodes. The alternating electric field between them has a voltage of 1.5KV and an alternating frequency of 1000Hz....
Embodiment 3
[0038] (1) Sonicate graphite oxide powder in HF solution with a solution concentration of 4.5% for 0.7 minutes to remove impurities on the surface of graphite oxide, and finally rinse with deionized water to remove residual HF liquid. At an ambient pressure of 500 Pa, the purity is Dry the graphite powder under the protection of 99.9% argon gas. After removing impurities, dry it under the protection of argon gas for later use;
[0039] (2) Put the graphite powder material into the co-rotating screw extruder, set the temperature of the co-rotating screw extruder to 250°C, and the extrusion speed to 450 rpm / min, and obtain a finer solid product after grinding Graphite fine powder;
[0040] (3) The ultra-fine graphite powder is atomized with a high-pressure airflow, the nozzle pressure of the high-pressure airflow is 12MPa, the outlet flow rate is 24.4 m / s, and an alternating current of 15 A is provided between the two electrodes. The alternating electric field between them has ...
PUM
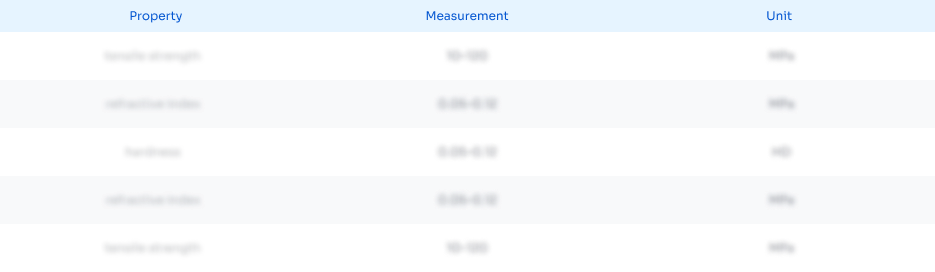
Abstract
Description
Claims
Application Information

- R&D Engineer
- R&D Manager
- IP Professional
- Industry Leading Data Capabilities
- Powerful AI technology
- Patent DNA Extraction
Browse by: Latest US Patents, China's latest patents, Technical Efficacy Thesaurus, Application Domain, Technology Topic, Popular Technical Reports.
© 2024 PatSnap. All rights reserved.Legal|Privacy policy|Modern Slavery Act Transparency Statement|Sitemap|About US| Contact US: help@patsnap.com