Spinning method of nickel base alloy bottom-carried cylindrical part
A technology of nickel-based alloys and processing methods, applied in metal processing equipment, forming tools, manufacturing tools, etc., can solve the problems of loss of continuity and integrity of metal fibers, reduction of material properties of cylindrical parts, and low stamping productivity, etc., to achieve Good plasticity, reduced material consumption, and improved productivity
- Summary
- Abstract
- Description
- Claims
- Application Information
AI Technical Summary
Problems solved by technology
Method used
Examples
Embodiment 1
[0022] Include the following steps:
[0023] (1) The material is GH4169 nickel-based alloy blank, with an outer diameter of Φ135 mm, a wall thickness of 14 mm, and a wall thickness difference of 0.1 mm;
[0024] (2) The mandrel is preheated to 400°C before spinning;
[0025] (3) The nickel-based alloy billet is heated to 700°C in a heating furnace for spinning and forming, using MoS2 lubricant, which is evenly applied to the mold and workpiece during spinning;
[0026] (4) Spinning forming is carried out on a spinning machine, and it is formed by a combination of general spinning and strong spinning. The specific parameters are as follows:
[0027] During the spinning process, oxygen-acetylene supplementary heating is used to ensure that the temperature of the nickel-based alloy blank is 700°C for spinning plastic forming, and the material is plastically formed in the α+β state. Feed rate f=50mm / min, wheel fillet radius r=15mm, wheel forming angle α=30°, withdrawal angle α=...
Embodiment 2
[0032] Include the following steps:
[0033] (1) The material is GH4169 nickel-based alloy blank, with an outer diameter of Φ140 mm, a wall thickness of 14.5 mm, and a wall thickness difference of 0.15 mm;
[0034] (2) The mandrel is preheated to 500°C before spinning;
[0035] (3) The nickel-based alloy sheet is rotated on the mandrel and heated to 850°C for spinning and forming. Glass lubricant is used and evenly applied to the blank before spinning;
[0036] (4) Spinning forming is carried out on a spinning machine, and it is formed by a combination of general spinning and strong spinning. The specific parameters are as follows:
[0037] During the spinning process, oxygen-acetylene supplementary heating is used to ensure that the temperature of the nickel-based alloy blank is 850°C for spinning plastic forming, and the material is plastically formed in the α+β state. The spindle speed is n=250r / min, and the spinning wheel is longitudinal Feed rate f=140mm / min, wheel fil...
Embodiment 3
[0042] Include the following steps:
[0043] (1) The material is GH4169 nickel-based alloy blank, with an outer diameter of Φ145 mm, a wall thickness of 15 mm, and a wall thickness difference of 0.2 mm;
[0044] (2) The mandrel is preheated to 600°C before spinning;
[0045] (3) The nickel-based alloy sheet is rotated on the mandrel and heated to 985°C for spinning and forming. Glass lubricant is used and evenly applied to the blank before spinning;
[0046] (4) Spinning forming is carried out on a spinning machine, and it is formed by a combination of general spinning and strong spinning. The specific parameters are as follows:
[0047] During the spinning process, oxygen-acetylene supplementary heating is used to ensure that the temperature of the nickel-based alloy blank is 985°C for spinning plastic forming, and the material is plastically formed in the α+β state. Feed rate f=150mm / min, wheel fillet radius r=30mm, wheel forming angle α=30°, withdrawal angle α=10°. Use ...
PUM
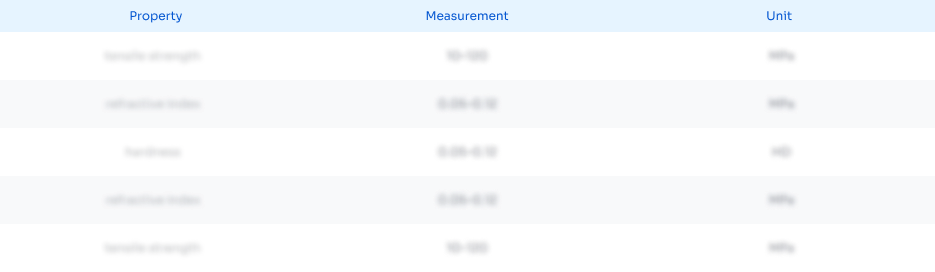
Abstract
Description
Claims
Application Information

- R&D
- Intellectual Property
- Life Sciences
- Materials
- Tech Scout
- Unparalleled Data Quality
- Higher Quality Content
- 60% Fewer Hallucinations
Browse by: Latest US Patents, China's latest patents, Technical Efficacy Thesaurus, Application Domain, Technology Topic, Popular Technical Reports.
© 2025 PatSnap. All rights reserved.Legal|Privacy policy|Modern Slavery Act Transparency Statement|Sitemap|About US| Contact US: help@patsnap.com