Preparation method of copper-based friction material with uniformly-distributed ferrum phase
A friction material and uniform distribution technology, applied in chemical instruments and methods, metal processing equipment, transportation and packaging, etc., can solve the problems of limited friction performance, uneven distribution, and inability to fully exert the excellent characteristics of iron phase, etc., to achieve Excellent friction and wear properties, the effect of improving the interface bonding strength
- Summary
- Abstract
- Description
- Claims
- Application Information
AI Technical Summary
Problems solved by technology
Method used
Image
Examples
Embodiment 1
[0014] 1. Prepare raw materials: copper-iron alloy powder with a mass ratio of 70%, 7% tin powder, 3% nickel powder, 7% graphite powder (flaky), 5% silica powder, 1% molybdenum disulfide, 7% Mullite;
[0015] 2. Pour the above powder into the improved double-cone mixer. The mixing cylinder rotates continuously to turn the material. The high-pressure gas pressure is about 0.1MPa. The sprayed adhesive lubricant solution forms a mist, which is mixed with the turned material Full contact, mixing for 8 hours;
[0016] 3. The uniformly mixed powder is cold-pressed, and the pressure is 400MPa;
[0017] 4. Sinter the cold green body in a hot-press sintering furnace, heat it to 850°C, sinter it in a hydrogen-nitrogen mixed gas, keep it warm for 180 minutes, and keep the hot-pressing pressure at 2MPa constant;
[0018] 5. Cool to below 100°C and take out, keep the pressure constant during the cooling process.
Embodiment 2
[0020] 1. Prepare raw materials: copper-iron alloy powder with a mass ratio of 73%, 7% tin powder, 3% nickel powder, 7% graphite powder (flaky), 2% silicon dioxide powder, 1% molybdenum disulfide, 7% Mullite;
[0021] 2. Pour the above powder into the improved double-cone mixer. The mixing cylinder rotates continuously to turn the material. The high-pressure gas pressure is about 0.1MPa. The sprayed adhesive lubricant solution forms a mist, which is mixed with the turned material Full contact, mixing for 8 hours;
[0022] 3. The uniformly mixed powder is cold-pressed, and the pressure is 400MPa;
[0023] 4. Sinter the cold green body in a hot-press sintering furnace, heat it to 880°C, sinter in a hydrogen-nitrogen mixed gas, keep it warm for 160 minutes, and keep the hot-press pressure at 2.3MPa, which is constant;
[0024] 5. Cool to below 100°C and take out, keep the pressure constant during the cooling process.
Embodiment 3
[0026] 1. Prepare raw materials: copper-iron alloy powder with a mass ratio of 77%, 5% tin powder, 2% nickel powder, 5% graphite powder (flaky), 3% silicon dioxide powder, 1% molybdenum disulfide, 7% Mullite;
[0027] 2. Pour the above powder into the improved double-cone mixer. The mixing cylinder rotates continuously to turn the material. The high-pressure gas pressure is about 0.1MPa. The sprayed adhesive lubricant solution forms a mist, which is mixed with the turned material Full contact, mixing for 8 hours;
[0028] 3. The uniformly mixed powder is cold-pressed, and the pressure is 400MPa;
[0029] 4. Sinter the cold green body in a hot-press sintering furnace, heat it to 920°C, sinter in a hydrogen-nitrogen mixed gas, keep it warm for 140 minutes, and keep the hot-press pressure at 2.7MPa, which is constant;
[0030] 5. Cool to below 100°C and take out, keep the pressure constant during the cooling process.
PUM
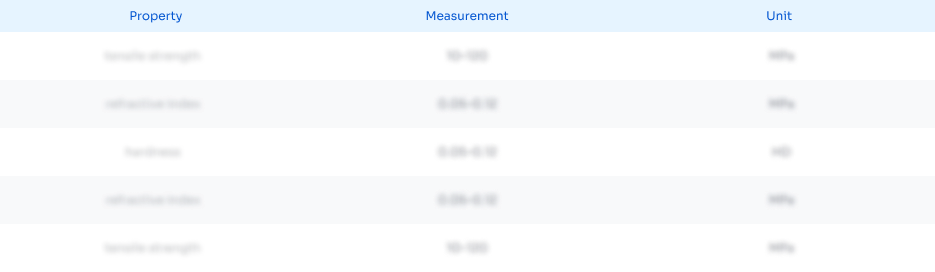
Abstract
Description
Claims
Application Information

- R&D
- Intellectual Property
- Life Sciences
- Materials
- Tech Scout
- Unparalleled Data Quality
- Higher Quality Content
- 60% Fewer Hallucinations
Browse by: Latest US Patents, China's latest patents, Technical Efficacy Thesaurus, Application Domain, Technology Topic, Popular Technical Reports.
© 2025 PatSnap. All rights reserved.Legal|Privacy policy|Modern Slavery Act Transparency Statement|Sitemap|About US| Contact US: help@patsnap.com