Environmentally friendly resin adhesive and preparation process thereof
An environment-friendly resin and resin binder technology, applied in the direction of adhesives, polymer adhesive additives, non-polymer adhesive additives, etc. Weather resistance, affecting the application of calcium silicate decorative boards and other issues, to achieve the effect of improving peel strength and adhesion performance, low cost, and good bonding performance
- Summary
- Abstract
- Description
- Claims
- Application Information
AI Technical Summary
Problems solved by technology
Method used
Examples
Embodiment 1
[0014] The resin binder component includes 30 parts of modified phenolic resin, 10 parts of tackifying resin, 5 parts of polylactic acid, 2 parts of polyvinyl alcohol, 3 parts of polyamide, 10 parts of lauryl dimethyl amine oxide, 5 parts of linoleic acid, 4 parts of silicon carbide, 5 parts of graphite.
[0015] The preparation process of the present embodiment comprises the following steps:
[0016] A. After mixing the modified phenolic resin, tackifying resin, polylactic acid and polyvinyl alcohol, add it into the heating tank and heat it to a molten state to obtain the mixture A;
[0017] B. Add silicon carbide and graphite into the mixture A, and stir thoroughly after mixing, the stirring speed is 2000 rpm, and the time is 20min, and the mixture B is obtained;
[0018] C. Add polyamide, lauryl dimethyl amine oxide, and linolenic acid to the mixture B. After mixing, add it to the reaction kettle for heating and stirring. The heating temperature is 60°C, and the stirring r...
Embodiment 2
[0020] The resin binder component includes 50 parts of modified phenolic resin, 20 parts of tackifying resin, 18 parts of polylactic acid, 8 parts of polyvinyl alcohol, 12 parts of polyamide, 20 parts of lauryl dimethyl amine oxide, 10 parts of linoleic acid, 12 parts of silicon carbide, 10 parts of graphite.
[0021] The preparation process of the present embodiment comprises the following steps:
[0022] A. After mixing the modified phenolic resin, tackifying resin, polylactic acid and polyvinyl alcohol, add it into the heating tank and heat it to a molten state to obtain the mixture A;
[0023] B. Add silicon carbide and graphite into the mixture A, and stir thoroughly after mixing, the stirring speed is 2000 rpm, and the time is 20min, and the mixture B is obtained;
[0024] C. Add polyamide, lauryl dimethyl amine oxide, and linolenic acid to the mixture B. After mixing, add it to the reaction kettle for heating and stirring. The heating temperature is 60°C, and the stirr...
Embodiment 3
[0026] The resin binder components include 35 parts of modified phenolic resin, 12 parts of tackifying resin, 7 parts of polylactic acid, 3 parts of polyvinyl alcohol, 5 parts of polyamide, 12 parts of lauryl dimethyl amine oxide, 6 parts of linoleic acid, 5 parts of silicon carbide, 5 parts of graphite.
[0027] The preparation process of the present embodiment comprises the following steps:
[0028] A. After mixing the modified phenolic resin, tackifying resin, polylactic acid and polyvinyl alcohol, add it into the heating tank and heat it to a molten state to obtain the mixture A;
[0029] B. Add silicon carbide and graphite into the mixture A, and stir thoroughly after mixing, the stirring speed is 2000 rpm, and the time is 20min, and the mixture B is obtained;
[0030] C. Add polyamide, lauryl dimethyl amine oxide, and linolenic acid to the mixture B. After mixing, add it to the reaction kettle for heating and stirring. The heating temperature is 60°C, and the stirring r...
PUM
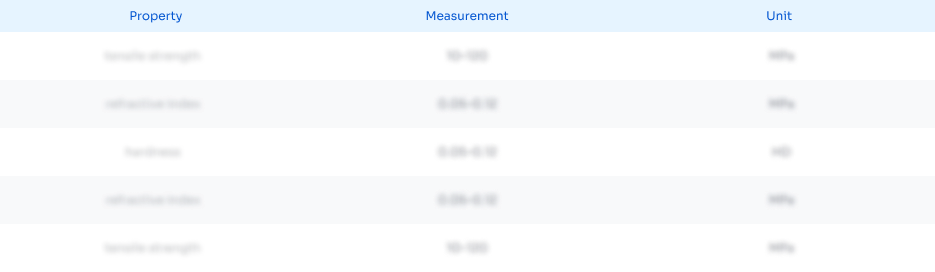
Abstract
Description
Claims
Application Information

- R&D
- Intellectual Property
- Life Sciences
- Materials
- Tech Scout
- Unparalleled Data Quality
- Higher Quality Content
- 60% Fewer Hallucinations
Browse by: Latest US Patents, China's latest patents, Technical Efficacy Thesaurus, Application Domain, Technology Topic, Popular Technical Reports.
© 2025 PatSnap. All rights reserved.Legal|Privacy policy|Modern Slavery Act Transparency Statement|Sitemap|About US| Contact US: help@patsnap.com