Thermoplastic fiber enhanced composite material, preparation method and application
A technology for reinforcing composite materials and thermoplastic fibers, applied in the field of materials, can solve the problems of low performance, high molding temperature of high-performance thermoplastic resin, poor adhesion, etc. performance and improved service life
- Summary
- Abstract
- Description
- Claims
- Application Information
AI Technical Summary
Problems solved by technology
Method used
Image
Examples
Embodiment 1
[0053] The preparation method of thermoplastic fiber reinforced composite material comprises the following steps:
[0054] (1) Get the raw material thermoplastic PP fiber fabric and thermoplastic PP resin film, and according to the designed fiber volume content, the thermoplastic PP fiber fabric and the thermoplastic PP resin film are cross-stacked;
[0055] (2) Melt and infiltrate thermoplastic resin into thermoplastic fiber fabric under high temperature and high pressure: the adopted molding temperature is about 280°C, which is higher than the melting point of thermoplastic resin; the pressure used for molding is 5-10MPa per unit area;
[0056] (3) Cooling to about 55° C. to obtain a thermoplastic fiber-reinforced prepreg / sheet.
[0057] The properties of the obtained thermoplastic fiber reinforced prepreg were tested, and the following data were obtained:
[0058] Using the experimental test standards for composite materials, prepare standard-sized splines, paste strain ga...
Embodiment 2
[0062] The shell of the trolley case is prepared by using thermoplastic fiber reinforced composite material as raw material, and the specific method is as follows:
[0063] Using thermoplastic PP fiber fabric and PP plastic film as raw materials, a full thermoplastic composite trolley case shell with lining was prepared.
[0064] The specific steps are:
[0065] as attached figure 1 As shown, the PP plastic film ①, PP fiber fabric ② and lining / lining ③ are layered according to the design, and the whole is passed through the upper and lower heating and pressing rollers ④, and the plastic film melts and infiltrates the fiber fabric to prepare the thermoplastic fiber reinforced composite material prepreg / Sheet ⑤, cut the thermoplastic fiber reinforced composite material prepreg / sheet ⑤ to the required size, and after softening by heating on the heating plate ⑥, it is formed under the pressure of the upper and lower molding die ⑦, and it can be cooled down The PP fiber-reinfor...
PUM
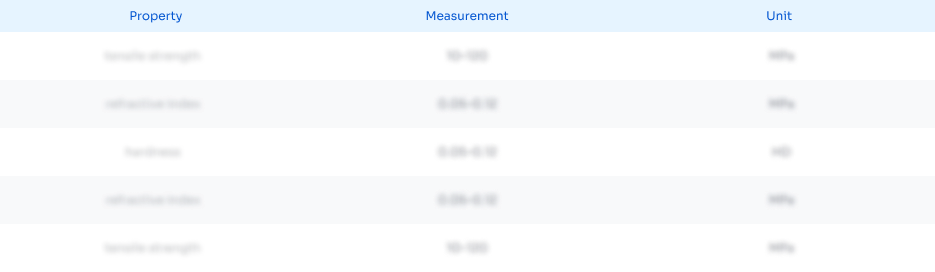
Abstract
Description
Claims
Application Information

- R&D
- Intellectual Property
- Life Sciences
- Materials
- Tech Scout
- Unparalleled Data Quality
- Higher Quality Content
- 60% Fewer Hallucinations
Browse by: Latest US Patents, China's latest patents, Technical Efficacy Thesaurus, Application Domain, Technology Topic, Popular Technical Reports.
© 2025 PatSnap. All rights reserved.Legal|Privacy policy|Modern Slavery Act Transparency Statement|Sitemap|About US| Contact US: help@patsnap.com