Heat treatment method for improving hardness uniformity of wear-resistant steel surface
A heat treatment method and surface hardness technology, which is applied in the field of wear-resistant steel, can solve the problems of poor unevenness, low cooling speed, and small contact water of thin-gauge products, so as to solve the problem of uneven hardness, improve the qualified rate of plate shape, and reduce the roll The effect of track speed
- Summary
- Abstract
- Description
- Claims
- Application Information
AI Technical Summary
Problems solved by technology
Method used
Image
Examples
Embodiment Construction
[0024] The present invention will be described in detail through specific embodiments below.
[0025] In order to realize the invention, the wear-resistant steel whose surface is 16-50 mm without quenching watermark and whose hardness fluctuation of the whole steel plate is within HBW3 has a high degree of uniformity, the hardness is between HBW350-HBW530, and the unevenness of the steel plate reaches 0-3mm / m, A wear-resistant steel plate with tempered martensite structure was obtained. The present invention performs quenching and tempering treatment on the rolled steel plate according to the heat treatment process parameters in Table 1. The main process parameters such as quenching heating temperature and tempering temperature of the steel plate are shown in Table 1. Corresponding properties of steel plates such as testing and grinding thickness, Brinell hardness and its fluctuation value, unevenness of steel plates are also listed in Table 2.
[0026] Table 1 Main producti...
PUM
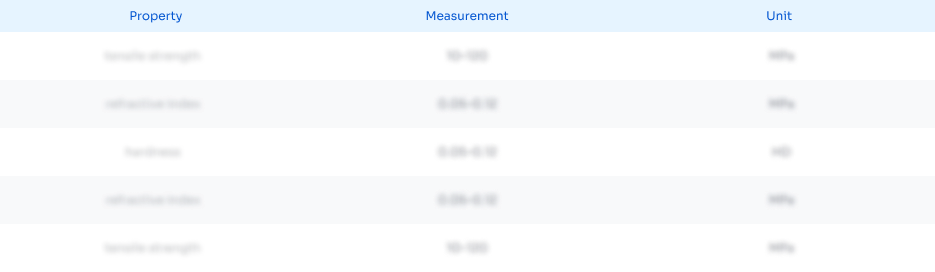
Abstract
Description
Claims
Application Information

- Generate Ideas
- Intellectual Property
- Life Sciences
- Materials
- Tech Scout
- Unparalleled Data Quality
- Higher Quality Content
- 60% Fewer Hallucinations
Browse by: Latest US Patents, China's latest patents, Technical Efficacy Thesaurus, Application Domain, Technology Topic, Popular Technical Reports.
© 2025 PatSnap. All rights reserved.Legal|Privacy policy|Modern Slavery Act Transparency Statement|Sitemap|About US| Contact US: help@patsnap.com