Thin-gauge and high-strength hot-rolled steel strip for cold forming and production method of thin-gauge and high-strength hot-rolled steel strip
A production method and high-strength technology, applied in the field of hot-rolled steel strip, can solve the problems of very strict smelting process requirements and difficult control of plate shape and coil shape.
- Summary
- Abstract
- Description
- Claims
- Application Information
AI Technical Summary
Problems solved by technology
Method used
Image
Examples
Embodiment Construction
[0050] The present invention will be further described in detail below in conjunction with specific examples.
[0051] The thin-gauge high-strength hot-rolled steel strip for cold forming provided by the present invention has the following chemical composition weight contents: C: 0.04-0.10%, Si: 0.05-0.25%, Mn: 1.0-1.5%, P≤0.010%, S≤0.008%, Nb: 0.03~0.07%, V: 0.08~0.20%, Ti: 0.10~0.20%, Mo: 0.05~0.20%, N≤40ppm, O≤50ppm, the balance is Fe and unavoidable impurities . The specific values of the chemical components in each embodiment are shown in Table 1.
[0052] The chemical composition (wt.%) of each embodiment steel strip of table 1
[0053]
[0054] The production process of the hot-rolled high-strength steel strip includes: blast furnace molten iron→desulfurization of molten iron→converter top-bottom composite blowing→argon blowing→ladle furnace→vacuum treatment→continuous casting→slab inspection→stacking slow cooling→slab heating →Controlled rolling→Controlled cool...
PUM
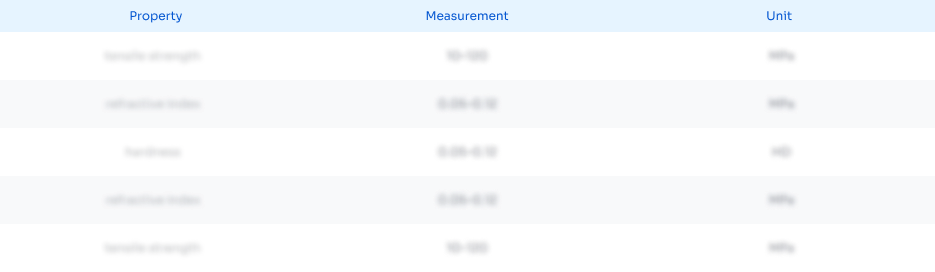
Abstract
Description
Claims
Application Information

- R&D
- Intellectual Property
- Life Sciences
- Materials
- Tech Scout
- Unparalleled Data Quality
- Higher Quality Content
- 60% Fewer Hallucinations
Browse by: Latest US Patents, China's latest patents, Technical Efficacy Thesaurus, Application Domain, Technology Topic, Popular Technical Reports.
© 2025 PatSnap. All rights reserved.Legal|Privacy policy|Modern Slavery Act Transparency Statement|Sitemap|About US| Contact US: help@patsnap.com