Preparation method of magnetic water treatment filler
A magnetic water and magnetic powder technology is applied in biological water/sewage treatment, water/sludge/sewage treatment, chemical instruments and methods, etc. It can solve problems such as long start-up time, slow film formation, and poor biocompatibility, and achieve Reduce investment cost, increase load, and have good biocompatibility
- Summary
- Abstract
- Description
- Claims
- Application Information
AI Technical Summary
Problems solved by technology
Method used
Examples
Embodiment 1
[0039] Weigh 0.8 kg of ferroferric oxide magnetic powder, pulverize the magnetic powder and pass it through a 500-mesh sieve, take the silane coupling agent KH-5500.1 kg, dilute it with 1 times the amount of liquid paraffin, add it to the above-mentioned magnetic powder, stir and mix well for use; Take 0.3 kg of calcium carbonate, pulverize the calcium carbonate and pass it through a 300-mesh sieve for later use. Add 3 kg of polypropylene resin to a high-speed mixer. After heating to 170°C to melt, add the processed magnetic powder and calcium carbonate, stir and mix. The mixture is added to the bin of the twin-screw granulator, and the granulation process is completed by the twin-screw granulator to form 7mm granules. Add the pellets to the silo of the twin-screw extruder, set the feed temperature to 160-170°C, the discharge temperature to 170-190°C, and the injection pressure to 80-90MPa, extrude into a continuous extrusion profile. After cooling, It is cut into a filler with...
Embodiment 2
[0041] Weigh 0.4kg of ferroferric oxide magnetic powder, pulverize the magnetic powder and pass it through a 500-mesh sieve, take 0.05kg of sodium stearate, dilute it with 1 times the amount of liquid paraffin, add it to the magnetic powder, stir and mix evenly for later use, weigh the carbonic acid Calcium 0.1kg, pulverized calcium carbonate and passed through a 300-mesh sieve for later use. Add 3.6kg of polyethylene resin to a high-speed mixer. After heating to 130°C to melt, add the processed magnetic powder and calcium carbonate, stir and mix. The mixed material is added to the bin of the twin-screw granulator, and the granulation process is completed by the twin-screw granulator to form 5mm granules. Add the pellets to the silo of the twin-screw extruder, set the feeding temperature to 125-140°C, the discharging temperature to 140-160°C, and the injection pressure to be 60-80MPa, and extrude them into continuous extrusion profiles. After cooling, It is cut into fillers wit...
Embodiment 3
[0043] Weigh 0.3 kg of ferroferric oxide magnetic powder, pulverize the magnetic powder and pass it through a 500-mesh sieve, take 0.03 kg of titanate coupling agent, dilute with 1 times the amount of liquid paraffin, add to the above-mentioned magnetic powder, stir and mix evenly for use, weigh Take 0.2 kg of talc powder, pulverize the talc powder and pass it through a 300-mesh sieve for use. Add 0.7 kg of polyvinyl chloride resin to the high-speed mixer, heat to 185°C to melt, add the processed magnetic powder and talc powder, and stir Mix, add the mixture into the bin of the twin-screw granulator, and complete the granulation process through the twin-screw granulator to form 8mm particles. Add the pellets to the silo of the twin-screw extruder, set the feeding temperature to 190-210°C, the discharging temperature to 200-230°C, and the injection pressure to be 70-80MPa, and extrude them into continuous extrusion profiles. After cooling, It is cut into fillers with a length of...
PUM
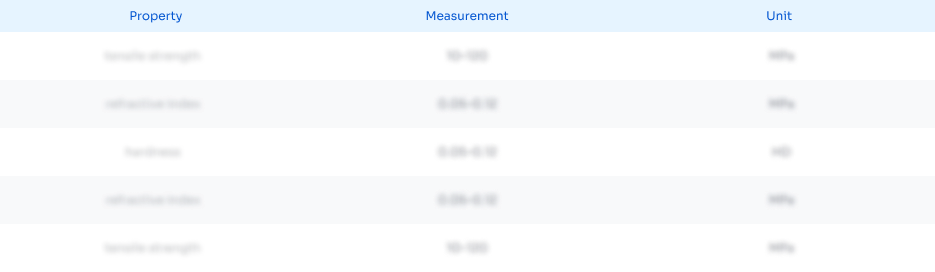
Abstract
Description
Claims
Application Information

- R&D Engineer
- R&D Manager
- IP Professional
- Industry Leading Data Capabilities
- Powerful AI technology
- Patent DNA Extraction
Browse by: Latest US Patents, China's latest patents, Technical Efficacy Thesaurus, Application Domain, Technology Topic, Popular Technical Reports.
© 2024 PatSnap. All rights reserved.Legal|Privacy policy|Modern Slavery Act Transparency Statement|Sitemap|About US| Contact US: help@patsnap.com