Process for preparing aniline compounds through hydrogenation of nitrobenzene compounds in multistage fluidized bed
A technology of aniline compounds and nitrobenzenes, which is applied in the chemical industry, can solve the problems of large fluctuations in production tasks, gas velocity fluctuations, space velocity fluctuations of catalysts, narrow gas velocity ranges, complex structures, etc., and achieve multi-stage fluidized bed structure reduction , the proportion of qualified products increased, and the effect of reducing the difficulty of control operations
- Summary
- Abstract
- Description
- Claims
- Application Information
AI Technical Summary
Problems solved by technology
Method used
Image
Examples
Embodiment 1
[0023] The gas inlet 2, the gas outlet 6, the component system 4, the heat exchange system 3, the transverse porous distribution plate 5, the overflow pipe 7, etc. figure 1 A fluidized bed 1 consisting of two stages.
[0024] Fill the two-stage fluidized bed with double-sieve catalyst (nickel / silicon oxide, particle size distribution of 10-400 microns, double-sieve distribution with 60 microns, 200 microns as the peak center, and 60 microns as the peak center group The mass fraction in the catalyst is 10%), the catalyst and the multi-stage fluidized bed are heated to 180°C with high-temperature gas (air), and the oxygen content in the outlet gas of the fluidized bed is less than 0.5%. The catalyst was reduced at 180° C. for 10 hours at a gas velocity of 0.03 m / s by feeding a mixture of hydrogen and nitrogen (the volume content of hydrogen was 10%). Heat hydrogen together with nitrobenzene to 190°C, pass it into the fluidized bed, and control the catalyst space velocity to 0....
Embodiment 2
[0027] The gas inlet 2, the gas outlet 6, the component system 4, the heat exchange system 3, the transverse porous distribution plate 5, the overflow pipe 7, etc. figure 2 A fluidized bed 1 consisting of three stages.
[0028] Fill the three-stage fluidized bed with a double-sieve catalyst (copper-nickel / silica gel, particle size distribution of 10-350 microns, double-sieve distribution with 70 microns, 250 microns as the peak center, and a group with 70 microns as the peak center The mass fraction in the catalyst as a whole is 30%), the catalyst and the multi-stage fluidized bed are heated to 180° C. with high-temperature gas (nitrogen), and the oxygen in the outlet gas of the fluidized bed is purged by an inert gas (nitrogen). The content is less than 0.5%. The catalyst was reduced at 180° C. for 24 hours by feeding a mixture of hydrogen and nitrogen (the volume content of hydrogen was 10%), and the gas velocity was 0.05 m / s. Heat hydrogen together with methylnitrobenzen...
Embodiment 3
[0031] The gas inlet 2, the gas outlet 6, the component system 4, the heat exchange system 3, the transverse porous distribution plate 5, the overflow pipe 7, etc. image 3 A fluidized bed 1 consisting of four stages.
[0032]Fill the four-stage fluidized bed with double-sieve catalysts (gold-copper / alumina, particle size distribution of 15-450 microns, double-sieve distribution with 80 microns, 300 microns as the peak center, and 80 microns as the peak center The mass fraction of the component in the catalyst is 40%), the catalyst and the multi-stage fluidized bed are heated to 195 °C with high-temperature gas (air), and the fluidized bed outlet gas is purged by an inert gas (nitrogen or argon). The oxygen content is less than 0.5%. The catalyst was reduced at 200° C. for 12 hours by feeding a mixture of hydrogen and nitrogen (the volume content of hydrogen was 20%), and the gas velocity was 0.03 m / s. Heat hydrogen together with chloronitrobenzene to 200°C, pass it into the...
PUM
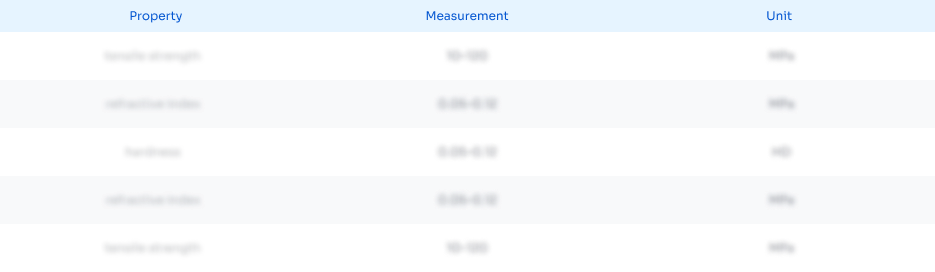
Abstract
Description
Claims
Application Information

- R&D
- Intellectual Property
- Life Sciences
- Materials
- Tech Scout
- Unparalleled Data Quality
- Higher Quality Content
- 60% Fewer Hallucinations
Browse by: Latest US Patents, China's latest patents, Technical Efficacy Thesaurus, Application Domain, Technology Topic, Popular Technical Reports.
© 2025 PatSnap. All rights reserved.Legal|Privacy policy|Modern Slavery Act Transparency Statement|Sitemap|About US| Contact US: help@patsnap.com