Intake valve for automobile engine
A technology for automobile engines and intake valves, which is applied in the direction of engine components, machines/engines, mechanical equipment, etc., can solve the problems of high cost of intake valves, achieve easy control of solidification speed, ensure solidification time, improve wear resistance and The effect of hardness
- Summary
- Abstract
- Description
- Claims
- Application Information
AI Technical Summary
Problems solved by technology
Method used
Examples
Embodiment 1
[0023] An intake valve for an automobile engine,
[0024] The intake valve manufacturing method includes the following steps: the intake valve includes a valve head and a valve stem, wherein the intake valve head is made of titanium alloy, and the intake valve stem is made of an iron-based alloy. First, an iron-based alloy rod with the same diameter is prepared. And titanium-based alloy rods, two rods are friction welded: firstly, at a speed of 1200rpm, a friction pressure of 20MPa, friction welding for 9s, and a friction feed rate of 0.6mm / s; then the speed is increased to 1900rpm, and the friction pressure is 75MPa. 15s, the friction feed rate is 0.4mm / s, then apply an upsetting pressure of 130MPa, hold the brake for 2 seconds, apply an upsetting pressure of 130MPa for another 8-s, and the upsetting deformation is 2.5mm, and the obtained welded rod The body is machined according to the size requirements of the intake valve head and rod to obtain the intake valve blank. The m...
Embodiment 2
[0032] An intake valve for an automobile engine,
[0033] The intake valve manufacturing method includes the following steps: the intake valve includes a valve head and a valve stem, wherein the intake valve head is made of titanium alloy, and the intake valve stem is made of an iron-based alloy. First, an iron-based alloy rod with the same diameter is prepared. And titanium-based alloy rods, two rods are friction welded: first, at a speed of 1220rpm, a friction pressure of 25MPa, friction welding for 10s, and a friction feed rate of 0.8mm / s; then the speed is increased to 1850rpm, friction pressure 80MPa, friction welding 12s, the friction feed rate is 0.5mm / s, then apply an upsetting pressure of 120MPa, hold the brake for 2 seconds, apply an upsetting pressure of 120MPa for another 9s, and the amount of upsetting deformation is 3mm, and the obtained welded rod body, according to The size of the intake valve head and stem requires machining and forming to obtain the intake va...
Embodiment 3
[0041] An intake valve for an automobile engine,
[0042] The intake valve manufacturing method includes the following steps: the intake valve includes a valve head and a valve stem, wherein the intake valve head is made of titanium alloy, and the intake valve stem is made of an iron-based alloy. First, an iron-based alloy rod with the same diameter is prepared. And titanium-based alloy rods, two rods are friction welded: first, at a speed of 1250rpm, a friction pressure of 24MPa, friction welding for 8s, and a friction feed rate of 0.7mm / s; then the speed is increased to 1880rpm, friction pressure 78MPa, friction welding 16s, the friction feed rate is 0.4mm / s, then apply an upsetting pressure of 125MPa, hold the brake for 2 seconds, apply an upsetting pressure of 125MPa for another 8s, and the amount of upsetting deformation is 3mm, and the obtained welded rod body, according to The size of the intake valve head and stem requires machining and forming to obtain the intake val...
PUM
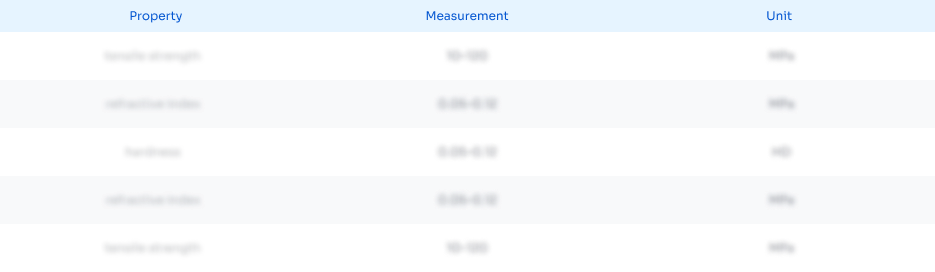
Abstract
Description
Claims
Application Information

- R&D Engineer
- R&D Manager
- IP Professional
- Industry Leading Data Capabilities
- Powerful AI technology
- Patent DNA Extraction
Browse by: Latest US Patents, China's latest patents, Technical Efficacy Thesaurus, Application Domain, Technology Topic, Popular Technical Reports.
© 2024 PatSnap. All rights reserved.Legal|Privacy policy|Modern Slavery Act Transparency Statement|Sitemap|About US| Contact US: help@patsnap.com