Stack box casting method of crusher hammerhead
A casting method and crusher technology are applied in the directions of casting molds, casting mold components, casting molding equipment, etc., to achieve the effects of improving quenching quality, improving productivity and simple operation process
- Summary
- Abstract
- Description
- Claims
- Application Information
AI Technical Summary
Problems solved by technology
Method used
Image
Examples
Embodiment 1
[0029] Such as figure 1 , figure 2 As shown, a stacked box casting method for hammerheads of crushers is carried out in sequence as follows:
[0030] A. Along the parting line of the hammer handle, the upper and lower molds are combined to form a hammer mold. There is a hollow part in the middle of the hammer mold. The hollow part is the shape of the hammer handle and the composite part. Manganese steel molten steel up to 1500°C is poured into the hammer mold from the gate, and the manganese steel contains C 0.75%, Si 0.2%, Mn 10.5%, Cr 0.5%, Mo 0.1%, Ni0.01%, Cu 0.01%, P 0.008%, S 0.008%, when cooled to 250°C, open the box, knock off the gate first, and then polish it to get a high manganese steel hammer handle;
[0031] B. Remove the impurities on the surface of the composite part of the high manganese steel hammer handle 4, put on the hammer head lost foam 5, then brush the hammer head lost foam 5 with a refractory coating, and bake the assembled hammer head model 3 in a...
Embodiment 2
[0041] A stacked box casting method for hammer heads of crushers, which is carried out in sequence as follows:
[0042] A. Along the parting line of the hammer handle, the upper and lower molds are combined to form a hammer mold. There is a hollow part in the middle of the hammer mold. The hollow part is the shape of the hammer handle and the composite part. Manganese steel molten steel up to 1525°C is poured into the hammer mold from the gate. The manganese steel contains C 1.025%, Si 0.5%, Mn 11.75%, Cr 1.25%, Mo0.1%, Ni 0.105%, Cu 0.055%, P 0.0085%, S 0.0085%, when cooled to 300°C, open the box, knock out the gate first, and then polish it smooth to get a high manganese steel hammer handle;
[0043] B. Remove the debris on the surface of the compound part of the high manganese steel hammer, put on the lost foam of the hammer head, and then brush the refractory coating on the lost foam of the hammer head, and bake the assembled hammer head model in a baking room at 55°C for ...
Embodiment 3
[0053] A stacked box casting method for hammer heads of crushers, which is carried out in sequence as follows:
[0054] A. Along the parting line of the hammer handle, the upper and lower molds are combined to form a hammer mold. There is a hollow part in the middle of the hammer mold. The hollow part is the shape of the hammer handle and the composite part. Manganese steel molten steel up to 1550°C is poured into the hammer mold from the gate. The manganese steel contains C 1.30%, Si 0.8%, Mn 13%, Cr 2%, Mo 0.1%, Ni0.2%, Cu 0.1%, P 0.009%, S 0.009%, when cooled to 350°C, open the box, knock out the gate first, and then polish it smooth to get a high manganese steel hammer handle;
[0055] B. Remove the sundries on the surface of the compound part of the high manganese steel hammer, put on the lost foam of the hammer head, and then brush the refractory coating on the lost foam of the hammer head, and bake the assembled hammer head model in a baking room at 60°C for 1 hour Or ...
PUM
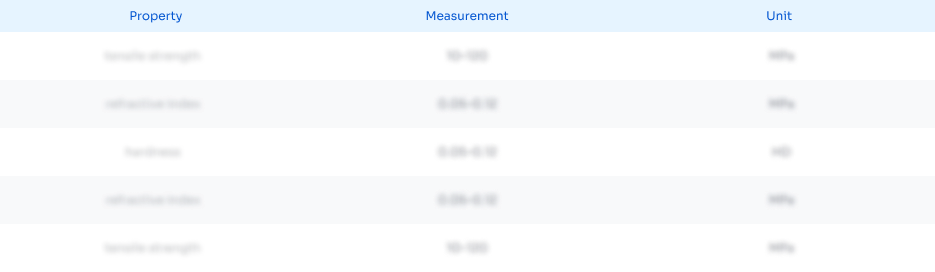
Abstract
Description
Claims
Application Information

- R&D
- Intellectual Property
- Life Sciences
- Materials
- Tech Scout
- Unparalleled Data Quality
- Higher Quality Content
- 60% Fewer Hallucinations
Browse by: Latest US Patents, China's latest patents, Technical Efficacy Thesaurus, Application Domain, Technology Topic, Popular Technical Reports.
© 2025 PatSnap. All rights reserved.Legal|Privacy policy|Modern Slavery Act Transparency Statement|Sitemap|About US| Contact US: help@patsnap.com