Process for roller shaft neck abrasion repairing and complete equipment for process
A technology of wear repair and complete set of equipment, which is applied in the direction of metal material coating process, coating, etc., can solve the problems of not being perfect, reducing the strength of the journal, consuming a lot of manpower and material resources, etc., to achieve convenient support, avoid cracks, avoid Shedding effect
- Summary
- Abstract
- Description
- Claims
- Application Information
AI Technical Summary
Problems solved by technology
Method used
Image
Examples
Embodiment 1
[0039] The process used for roll journal wear repair includes the following steps:
[0040] a. Pretreatment: Degrease and derust the worn surface of the journal of the roller shaft, measure the size of the worn part of the journal, the size after the test is φ159.2mm, and the original size of the journal is The wear amount on one side of the diameter is 0.4-0.5mm, and a layer of laser cladding is applied.
[0041] b. Placement: According to the length of the roller shaft, adjust the roller table to a suitable distance to facilitate tooling, and hang the roller shaft on the complete set of equipment.
[0042] c. Cladding: Use a high-power semiconductor laser to clad wear-resistant alloy powder on the surface of the wear journal. The size of the wear-resistant alloy powder particles is 100-325 mesh. Its composition by weight percentage is as follows:
[0043] Carbon 0.4%, chromium 15%, nickel 5%, tungsten 2%, cobalt 14%, molybdenum 2%, silicon 1.2%, boron 1.2%, and the rest...
Embodiment 2
[0057] The process used for roll journal wear repair includes the following steps:
[0058] a. Pretreatment: Degreasing and derusting treatment on the worn surface of the journal of the roller shaft,) measuring the size of the worn part of the journal, the journal wears irregularly, the size is φ137.6-φ139.5mm, and the original size of the journal is The wear on one side of the diameter is 0.25-1.2mm, and the number of layers of laser cladding is different in different parts.
[0059] b. Placement: According to the length of the roller shaft, adjust the roller table to a suitable distance to facilitate tooling, and hang the roller shaft on the complete set of equipment.
[0060] c. Cladding: Use a high-power semiconductor laser to clad wear-resistant alloy powder on the surface of the wear journal. The size of the wear-resistant alloy powder particles is 100-325 mesh. Its composition by weight percentage is as follows:
PUM
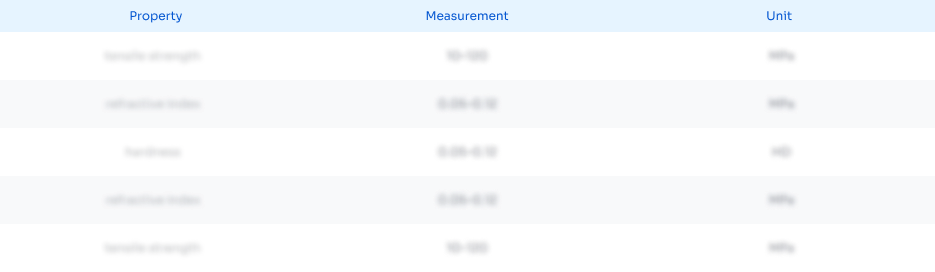
Abstract
Description
Claims
Application Information

- R&D Engineer
- R&D Manager
- IP Professional
- Industry Leading Data Capabilities
- Powerful AI technology
- Patent DNA Extraction
Browse by: Latest US Patents, China's latest patents, Technical Efficacy Thesaurus, Application Domain, Technology Topic, Popular Technical Reports.
© 2024 PatSnap. All rights reserved.Legal|Privacy policy|Modern Slavery Act Transparency Statement|Sitemap|About US| Contact US: help@patsnap.com