Preparation method of porous ceramic material rapidly formed based on photocuring
A technology of light-curing molding and porous ceramics, applied in the direction of additive processing, etc., can solve problems such as shape and structure optimization, application limitations, etc., and achieve the effect of high porosity
- Summary
- Abstract
- Description
- Claims
- Application Information
AI Technical Summary
Problems solved by technology
Method used
Image
Examples
preparation example Construction
[0029] see figure 1 , a method for preparing a porous ceramic material based on light-curing rapid prototyping provided by the present invention, which specifically includes the following steps:
[0030] 1) The photocurable resin prepolymer, reactive diluent and surface modifier are mechanically mixed to obtain a premixed liquid; the photocurable resin prepolymer, reactive diluent and surface modifier are respectively by weight :
[0031] Photocurable resin prepolymer: 0-100 parts
[0032] Active diluent: 1-40 parts
[0033] Surface modifier: 1-15 parts;
[0034] The photocurable resin prepolymer is selected from any one of epoxy resin and acrylic resin and a mixture of the two. The surface modifier is selected from any one or more mixtures of surfactants, coupling agents, unsaturated organic acids, and organic oligomers; the reactive diluent is an acrylate monomer; the acrylate Monomers are 1,6-ethylene glycol diacrylate, isobornyl acrylate, propoxylated neopentyl glycol...
Embodiment 1
[0041]First, 100 parts of 1,6-ethylene glycol diacrylate and propoxylated neopentyl glycol diacrylate are mixed in a mass ratio of 1:1, and 1 part of sodium dodecylbenzenesulfonate is fully mixed to obtain a pre- Mixed liquid; mix starch and alumina ceramic powder at the same time to obtain porous ceramic powder, wherein starch accounts for 1vol% of the porous ceramic powder; mix porous ceramic powder into the premixed liquid, and ball mill to obtain primary slurry, wherein the powder The addition amount is 40vol% of the primary slurry; Add the initiator 1-hydroxycyclohexyl phenyl ketone of premixed liquid quality 0.1wt% to obtain light-cured porous ceramic slurry; Put the prepared light-cured porous ceramic slurry into light In the curing molding equipment, the light-curing molding green body is obtained through light-curing 3D printing; the green body is heated to 550°C for 3 hours for degreasing, and heated to 1600°C for 2 hours for sintering. Alumina ceramic parts with uni...
Embodiment 2
[0043] Firstly, three different porous ceramic slurries were prepared for subsequent printing of parts with gradient pore microstructure.
[0044] Material 1: First, 100 parts of epoxy acrylic resin, such as dicyclopentadiene phenol type epoxy resin, 50 parts of 1,6-ethylene glycol diacrylate, and 5 parts of sodium dodecylbenzenesulfonate are fully mixed to obtain a pre- mixed liquid; at the same time, carbon powder and calcium phosphate ceramic powder are mixed to obtain porous ceramic powder, wherein carbon powder accounts for 30vol% of the porous ceramic powder; the porous ceramic powder is mixed into the premixed liquid, and ball milled to obtain primary slurry, wherein The powder is added in an amount of 70vol% of the primary slurry; a cationic initiator bis-2,6-difluoro-3-pyrrolephenylferrocene is added in an amount of 0.2wt% of the premix to obtain a light-cured porous ceramic slurry.
[0045] Material 2: First, 100 parts of 1,6-ethylene glycol diacrylate and 10 parts o...
PUM
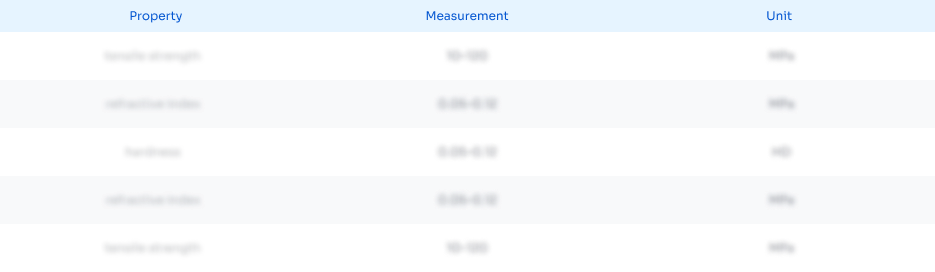
Abstract
Description
Claims
Application Information

- R&D Engineer
- R&D Manager
- IP Professional
- Industry Leading Data Capabilities
- Powerful AI technology
- Patent DNA Extraction
Browse by: Latest US Patents, China's latest patents, Technical Efficacy Thesaurus, Application Domain, Technology Topic, Popular Technical Reports.
© 2024 PatSnap. All rights reserved.Legal|Privacy policy|Modern Slavery Act Transparency Statement|Sitemap|About US| Contact US: help@patsnap.com