Preparation method and application of catalyst for preparing olefins
A catalyst and olefin technology, applied in chemical instruments and methods, heterogeneous catalyst chemical elements, physical/chemical process catalysts, etc., can solve problems such as poor high temperature resistance, low conversion rate, isopentene loss, etc., and achieve application wide range of effects
- Summary
- Abstract
- Description
- Claims
- Application Information
AI Technical Summary
Problems solved by technology
Method used
Examples
Embodiment 1
[0044] 40g γ-Al 2 o 3 Add to 50ml 15% nickel nitrate solution and let stand at room temperature for 6h, then filter, dry at 120°C for 2h, and roast at 400°C for 6h to obtain NiO / Al 2 o 3 .
[0045] Then the product was immersed in 40ml of 5% sodium silicate solution and 20% ammonium fluoride for 4h, filtered, dried at 160°C for 6h, and calcined at 400°C for 4h to obtain NiO / SiO 2 / F - / Al 2 o 3 .
[0046] NiO / SiO 2 / F - / Al 2 o 3 Add it to 50ml of 20% sulfuric acid solution, filter, dry at 100°C for 4h, and roast at 600°C for 5h. Promptly obtain the NiO / SiO of the present invention 2 / F - SO 4 2- / Al 2 o 3 .
[0047] Put 9g of catalyst into a micro-fixed bed reactor with a diameter of φ16mm, feed methyl tert-amyl ether with a liquid micro-sampling pump, control the liquid space velocity to 1h-1, the reaction temperature is 120°C, and the conversion rate of TAME is 95.5% , Isoamyl selectivity 96.8%, methanol selectivity 97.8%. The proportion of 2-methyl...
Embodiment 2
[0049] 40g γ-Al 2 o 3 Add it to 50ml 20% nickel nitrate solution and let stand at room temperature for 4h, then filter, dry at 100°C for 2h, and roast at 600°C for 6h to obtain NiO / Al 2 o 3 .
[0050] Then the product was immersed in 40ml of potassium silicate solution with a concentration of 3% and hydrofluoric acid with a concentration of 4% for 5h, filtered, dried at 120°C for 8h, and calcined at 300°C for 4h to obtain NiO / SiO 2 / F - / Al 2 o 3 .
[0051] NiO / SiO 2 / F - / Al 2 o 3 Add it to 30ml of 20% ammonium sulfate solution, filter, dry at 160°C for 3h, and roast at 500°C for 5h. Promptly obtain the NiO / SiO of the present invention 2 / F - / SO 4 2- / Al 2 o 3 .
[0052] Put 9g of catalyst into a micro-fixed bed reactor with a diameter of φ16mm, feed methyl tert-butyl ether with a liquid micro-sampling pump, control the liquid space velocity to 2h-1, the reaction temperature is 140°C, and the MTBE conversion rate is 97.6% , Isobutene selectivity 97.8%...
Embodiment 3
[0054] 40g γ-Al 2 o 3 Add it to 50ml 30% nickel sulfate solution and let stand at room temperature for 6h, then filter, dry at 100°C for 2h, and roast at 700°C for 6h to obtain NiO / Al 2 o 3 .
[0055] Then the product was immersed in 40ml of 10% ammonium fluorosilicate solution for 6h, filtered, dried at 120°C for 2h, and calcined at 400°C for 6h to obtain NiO / SiO 2 / F - / Al 2 o 3 .
[0056] NiO / SiO 2 / F - / Al 2 o 3 Add it to 50ml of 20% ammonium bisulfate solution, filter, dry at 100°C for 6h, and roast at 500°C for 5h. Promptly obtain the NiO / SiO of the present invention 2 / F - / SO 4 2- / Al 2 o 3 .
[0057] Put 9g of catalyst into a micro-fixed bed reactor with a diameter of φ16mm, feed methyl tert-amyl ether with a liquid micro-sampling pump, control the liquid space velocity to 3h-1, the reaction temperature is 160°C, and the conversion rate of TAME is 97.5% , The selectivity of isopentene is 97.6%, and the selectivity of methanol is 98.7%. The pro...
PUM
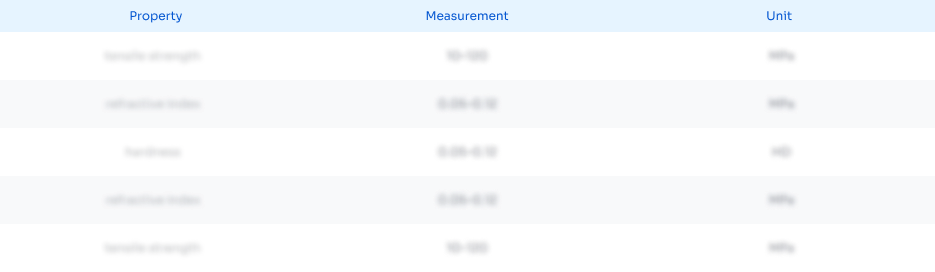
Abstract
Description
Claims
Application Information

- R&D
- Intellectual Property
- Life Sciences
- Materials
- Tech Scout
- Unparalleled Data Quality
- Higher Quality Content
- 60% Fewer Hallucinations
Browse by: Latest US Patents, China's latest patents, Technical Efficacy Thesaurus, Application Domain, Technology Topic, Popular Technical Reports.
© 2025 PatSnap. All rights reserved.Legal|Privacy policy|Modern Slavery Act Transparency Statement|Sitemap|About US| Contact US: help@patsnap.com