High-carbon, low-chromium and low-tungsten grinding ball high in hardness and resistant to impact and preparation method thereof
A high-hardness, impact-resistant technology, applied in the field of wear-resistant balls, to achieve the effect of extending service life, improving wear resistance and corrosion resistance
- Summary
- Abstract
- Description
- Claims
- Application Information
AI Technical Summary
Problems solved by technology
Method used
Examples
Embodiment 1
[0020] A high-carbon, low-chromium, low-tungsten, high-hardness and impact-resistant wear-resistant ball proposed by the present invention has the following weight percentages of its components: C: 0.95%, Cr: 0.65%, Si: 2.15%, Mn: 0.7%, Mo: 0.5%, Ni: 0.55%, Rare Earth: 0.175%, V: 0.055%, B: 0.25%, Ti: 0.055%, W: 0.20%, Nb: 0.3%, Ta: 0.07%, Al: 0.06%, Cu: 0.9%, S: 0.025%, P: 0.015%, and the balance is Fe and unavoidable impurities.
Embodiment 2
[0022] A method for preparing a high-carbon, low-chromium, low-tungsten, high-hardness and impact-resistant wear-resistant ball of the present invention comprises the following steps:
[0023] S1. Iron block, carbon powder, chromium ingot, silicon powder, manganese block, molybdenum ingot, nickel block, vanadium ingot, boron block, titanium powder, tungsten block, niobium block, thallium ingot, aluminum ingot, copper block, sulfur powder Smelting with phosphorus powder at a melting temperature of 1400°C to obtain alloy liquid, and then adding rare earth for spheroidization treatment at a temperature of 1550°C;
[0024] S2. Carry out refining desulfurization and deoxidation to the spheroidized alloy liquid in S1, and perform detection. The alloy liquid includes the following components by weight percentage: C: 0.85%, Cr: 0.8%, Si: 1.4%, Mn: 0.8% , Mo: 0.4%, Ni: 0.65%, Rare Earth: 0.05%, V: 0.08%, B: 0.15%, Ti: 0.10%, W: 0.15%, Nb: 0.4%, Ta: 0.02%, Al: 0.08% , Cu: 0.6%, S: 0.03...
Embodiment 3
[0027] A method for preparing a high-carbon, low-chromium, low-tungsten, high-hardness and impact-resistant wear-resistant ball of the present invention comprises the following steps:
[0028] S1. Iron block, carbon powder, chromium ingot, silicon powder, manganese block, molybdenum ingot, nickel block, vanadium ingot, boron block, titanium powder, tungsten block, niobium block, thallium ingot, aluminum ingot, copper block, sulfur powder Smelting with phosphorus powder at a melting temperature of 1450°C to obtain an alloy solution, and then adding rare earth for spheroidization treatment at a temperature of 1450°C;
[0029] S2. Carry out refining desulfurization and deoxidation to the alloy liquid that has been spheroidized in S1, and perform detection. The alloy liquid includes the following components by weight percentage: C: 1.05%, Cr: 0.5%, Si: 2.9%, Mn: 0.6% , Mo: 0.6%, Ni: 0.45%, Rare Earth: 0.30%, V: 0.03%, B: 0.35%, Ti: 0.01%, W: 0.25%, Nb: 0.2%, Ta: 0.12%, Al: 0.04% ...
PUM
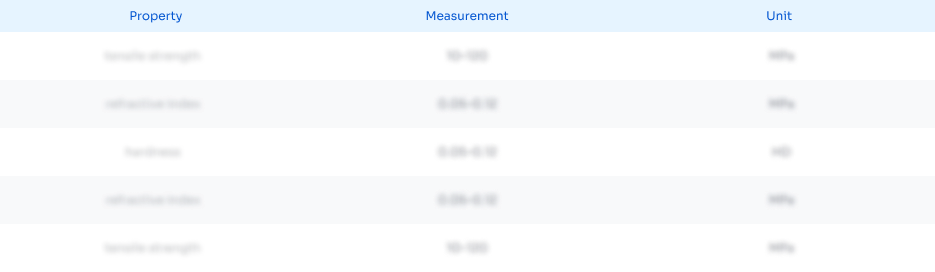
Abstract
Description
Claims
Application Information

- R&D Engineer
- R&D Manager
- IP Professional
- Industry Leading Data Capabilities
- Powerful AI technology
- Patent DNA Extraction
Browse by: Latest US Patents, China's latest patents, Technical Efficacy Thesaurus, Application Domain, Technology Topic, Popular Technical Reports.
© 2024 PatSnap. All rights reserved.Legal|Privacy policy|Modern Slavery Act Transparency Statement|Sitemap|About US| Contact US: help@patsnap.com