Borosilicate fluorescent glass with high heat conductivity coefficient and preparation method thereof
A fluorescent glass and borosilicate technology, applied in the field of materials science, can solve the problems affecting the luminous efficiency and service life, light decay, and color coordinates of LED light sources, and achieve good chemical stability, mechanical strength, and thermal stability. Good, avoid the effect of easy moisture
- Summary
- Abstract
- Description
- Claims
- Application Information
AI Technical Summary
Problems solved by technology
Method used
Image
Examples
Embodiment 1
[0025] Composition is as shown in 4# in table 1, and concrete preparation process is as follows:
[0026] According to the molar percentage of the 4# glass composition in Table 1, calculate the weight of the corresponding components, weigh each raw material and mix them evenly; put the mixture into a corundum crucible and melt it in a silicon carbide rod electric furnace at 1050 ° C ~ 1100 ° C , clarified for 15 minutes after complete melting, and poured the molten glass liquid into distilled water at room temperature; after a little cooling, it was quickly moved into a drying box for drying, and after drying, it was ground into powder, d 50 Around 12 μm. The glass powder and Ce:YAG phosphor were mixed evenly according to the mass ratio of 20:1 and placed in a muffle furnace at 580°C for sintering. After 15 minutes, the sample was taken out for cutting, grinding and polishing for subsequent testing.
[0027] The test results for this glass are as follows:
[0028] Process th...
Embodiment 2
[0030] Composition is as shown in 7# in table 1, and concrete preparation process is as follows:
[0031] According to the molar percentage of the 7# glass composition in Table 1, calculate the weight of each composition, weigh each raw material and mix them evenly; put the mixture into a corundum crucible and melt it in a silicon carbide rod electric furnace at 1050°C to 1100°C , clarified for 15 minutes after complete melting, and poured the molten glass liquid into distilled water at room temperature; after a little cooling, it was quickly moved into a drying box for drying, and after drying, it was ground into powder, d 50 Around 12 μm. The glass powder and Ce:YAG phosphor were mixed evenly according to the mass ratio of 20:1 and placed in a muffle furnace at 580°C for sintering. After 15 minutes, the sample was taken out for cutting, grinding and polishing for subsequent testing.
[0032] The test results for this glass are as follows:
[0033] Process the sample into a...
Embodiment 3
[0035] Composition is as shown in 11# in table 1, and concrete preparation process is as follows:
[0036] According to the molar percentage of the 11# glass composition in Table 1, calculate the weight of each composition, weigh each raw material and mix them evenly; put the mixture into a corundum crucible and melt it in a silicon carbide rod electric furnace at 1050°C to 1100°C , clarified for 15 minutes after complete melting, and poured the molten glass liquid into distilled water at room temperature; after a little cooling, it was quickly moved into a drying box for drying, and after drying, it was ground into powder, d 50 Around 12 μm. The glass powder and Ce:YAG phosphor were mixed uniformly according to the mass ratio of 15:1 and placed in a muffle furnace at 580°C for sintering. After 15 minutes, the sample was taken out for cutting, grinding and polishing for subsequent testing.
[0037] The test results for this glass are as follows:
[0038] Process the sample i...
PUM
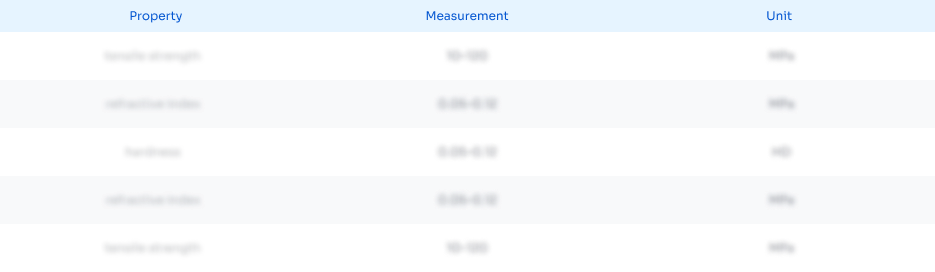
Abstract
Description
Claims
Application Information

- R&D Engineer
- R&D Manager
- IP Professional
- Industry Leading Data Capabilities
- Powerful AI technology
- Patent DNA Extraction
Browse by: Latest US Patents, China's latest patents, Technical Efficacy Thesaurus, Application Domain, Technology Topic, Popular Technical Reports.
© 2024 PatSnap. All rights reserved.Legal|Privacy policy|Modern Slavery Act Transparency Statement|Sitemap|About US| Contact US: help@patsnap.com