Aerogel composite fiber and manufacturing process thereof
A composite fiber and airgel technology, applied in the field of fiber products, can solve the problems of poor thermal insulation effect of fibers, affect the quality of garments, and easy to break, and achieve the effects of high thermal insulation performance, high toughness, and excellent thermal insulation
- Summary
- Abstract
- Description
- Claims
- Application Information
AI Technical Summary
Problems solved by technology
Method used
Examples
Embodiment 1
[0018] An airgel composite fiber, the airgel composite fiber includes airgel and PET, and the mass ratio of the airgel to PET is 0.1:5.
[0019] The manufacturing process of above-mentioned airgel composite fiber comprises the following steps:
[0020] 1) Mix the airgel PET masterbatch with the PET chip according to the ratio of 1:5, wherein, in the airgel PET masterbatch, the content of airgel is 10%, that is, the airgel and PET The mass ratio is 0.1:5; the mixed raw materials are dried to reduce the moisture in the airgel PET masterbatch and PET chips to 0.03%;
[0021] 2) Melting the mixed and dried airgel PET masterbatch and PET chips at a melt temperature of 285°C and a melt pressure of 1 MPa to form a spinning melt;
[0022] 3) Draw the spinning melt to form nascent fibers through the spinning assembly at a spinning speed of 1300m / min, blow and solidify at a temperature of 20°C, and cool and oil the cured nascent fibers;
[0023] 4) At a temperature of 110° C., the as-...
Embodiment 2
[0025] An airgel composite fiber, the airgel composite fiber includes airgel and PET, and the mass ratio of the airgel and PET is 0.2:5.
[0026] The manufacturing process of above-mentioned airgel composite fiber comprises the following steps:
[0027] 1) Mix the airgel PET masterbatch with the PET chip according to the ratio of 1:5, wherein, in the airgel PET masterbatch, the content of airgel is 20%, that is, the airgel and PET The mass ratio is 0.2:5; the mixed raw materials are dried to reduce the moisture in the airgel PET masterbatch and PET chips to 0.03%;
[0028] 2) Melting the mixed and dried airgel PET masterbatch and PET chips at a melt temperature of 290°C and a melt pressure of 2 MPa to form a spinning melt;
[0029] 3) Drawing the spinning melt at a spinning speed of 1500m / min through the spinneret assembly to form nascent fibers, blowing and solidifying at a temperature of 20°C, and cooling and oiling the cured nascent fibers;
[0030] 4) At a temperature of...
Embodiment 3
[0032] An airgel composite fiber, the airgel composite fiber includes airgel and PET, and the mass ratio of the airgel and PET is 0.1:10.
[0033] The manufacturing process of above-mentioned airgel composite fiber comprises the following steps:
[0034] 1) Mix the airgel PET masterbatch with the PET chip according to the ratio of 1:10, wherein, in the airgel PET masterbatch, the content of airgel is 10%, that is, the airgel and PET The mass ratio is 0.1:10; the mixed raw materials are dried to reduce the moisture in the airgel PET masterbatch and PET chips to 0.03%;
[0035] 2) Melting the mixed and dried airgel PET masterbatch and PET chips at a melt temperature of 285°C and a melt pressure of 1 MPa to form a spinning melt;
[0036] 3) Draw the spinning melt to form nascent fibers through the spinning assembly at a spinning speed of 1300m / min, blow and solidify at a temperature of 20°C, and cool and oil the cured nascent fibers;
[0037] 4) At a temperature of 110° C., the...
PUM
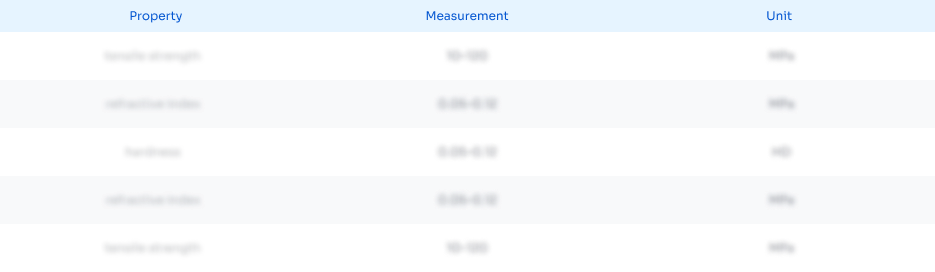
Abstract
Description
Claims
Application Information

- Generate Ideas
- Intellectual Property
- Life Sciences
- Materials
- Tech Scout
- Unparalleled Data Quality
- Higher Quality Content
- 60% Fewer Hallucinations
Browse by: Latest US Patents, China's latest patents, Technical Efficacy Thesaurus, Application Domain, Technology Topic, Popular Technical Reports.
© 2025 PatSnap. All rights reserved.Legal|Privacy policy|Modern Slavery Act Transparency Statement|Sitemap|About US| Contact US: help@patsnap.com