Wet process preparation technique of nickel
A preparation process and wet method technology, which is applied in the field of nickel wet preparation technology, can solve the problems of lengthiness, high processing cost, complicated process, etc., and achieve the effect of increasing catholyte flow rate, reducing cycle cost and optimizing cycle path
- Summary
- Abstract
- Description
- Claims
- Application Information
AI Technical Summary
Problems solved by technology
Method used
Image
Examples
Embodiment Construction
[0018] The implementation of the present application will be described in detail below with reference to the accompanying drawings and examples, so as to fully understand and implement the implementation process of how the present application uses technical means to solve technical problems and achieve technical effects.
[0019] Such as figure 1 As shown, the application includes the following steps:
[0020] Step 1: water quenching metallization of high nickel matte;
[0021] Step 2: use a ball mill to mill the water-quenched high nickel matte, enter the thickener for sedimentation after ball milling, and use the pressurized leaching solution and anolyte for slurrying the underflow to prepare ingredients;
[0022] Step 3: Carry out one stage of normal pressure, one stage of normal pressure leaching the pulp and enter the thickener after passing the pass, the pulp settles and separates the liquid from the solid, the overflow liquid is filtered to become a qualified finished ...
PUM
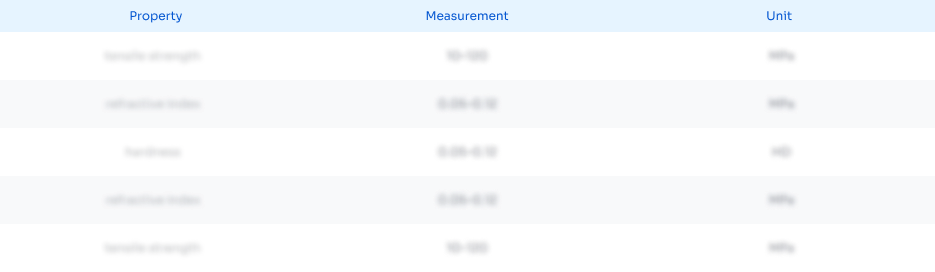
Abstract
Description
Claims
Application Information

- R&D
- Intellectual Property
- Life Sciences
- Materials
- Tech Scout
- Unparalleled Data Quality
- Higher Quality Content
- 60% Fewer Hallucinations
Browse by: Latest US Patents, China's latest patents, Technical Efficacy Thesaurus, Application Domain, Technology Topic, Popular Technical Reports.
© 2025 PatSnap. All rights reserved.Legal|Privacy policy|Modern Slavery Act Transparency Statement|Sitemap|About US| Contact US: help@patsnap.com