Preparation process for forge piece of discontinuous reinforcement aluminum-based composite
A composite material, enhanced aluminum-based technology, applied in metal processing equipment and other directions, can solve the problems of no free forging structure control method, huge difference in deformation uniformity, etc., to achieve easy control of deformation structure, improvement of microscopic uniformity, and improved The effect of forging efficiency
- Summary
- Abstract
- Description
- Claims
- Application Information
AI Technical Summary
Problems solved by technology
Method used
Examples
Embodiment 1
[0026] The 20vol.% SiCp / 2009Al billet was prepared by powder metallurgy method, and the rod was prepared by hot extrusion method, the size was φ150×3000mm, the extrusion temperature was 320°C, and the extrusion speed was 0.2mm / s. Cut the bar into φ150×300mm. Incubate at 480°C for 3 hours. Using 500 tons of hydraulic press for free forging, thickening along the direction of 300mm height, the deformation speed is 30mm / s, the deformation amount of each pass is 35%, and the final forging temperature is 430°C. Forging for 3 passes, holding the temperature at 480°C for 3 hours between each pass. The forging size of the workpiece is 150×150×230mm. There is no crack on the surface of the forged workpiece.
Embodiment 2
[0030] A 30vol.% SiCp / 2009Al ingot was prepared by powder metallurgy, and a rod was prepared by hot extrusion, with a size of φ350×1500mm, an extrusion temperature of 350°C, and an extrusion speed of 0.2mm / s. Cut the bar into φ350×350mm. Incubate at 480°C for 6 hours. Free forging with 800 tons hydraulic press. Coarse stewing along the height direction of 350mm, the deformation amount of each pass is 20%, the deformation speed is 25mm / s, and the final forging temperature is 430°C. Forging 4 times, between each pass at 480 ° C for 6 hours. The forging size of the workpiece is φ550×150mm. There are no cracks on the edge of the forged workpiece.
Embodiment 3
[0034]The 25vol.% SiCp / 2009Al billet was prepared by stirring casting method, and the rectangular material was prepared by hot extrusion method, the size was 150×200×3000mm, the extrusion temperature was 380°, and the extrusion speed was 0.2mm / s. Cut the rectangular bar into 150×200×300mm. Incubate at 460°C for 4 hours. Free forging with 800 tons hydraulic press. Forging along the height direction of 150mm, drawing along the width direction of 200mm, the deformation speed is 30mm / s, the deformation amount per pass is 30%, and the final forging temperature is 420°C. Forging 2 passes, between each pass at 460 ° C for 4 hours. The forging size of the workpiece is 70×350×350mm. There is no crack on the surface of the forged workpiece.
PUM
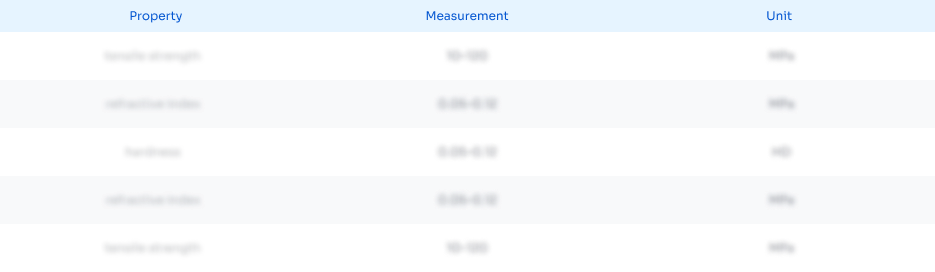
Abstract
Description
Claims
Application Information

- R&D
- Intellectual Property
- Life Sciences
- Materials
- Tech Scout
- Unparalleled Data Quality
- Higher Quality Content
- 60% Fewer Hallucinations
Browse by: Latest US Patents, China's latest patents, Technical Efficacy Thesaurus, Application Domain, Technology Topic, Popular Technical Reports.
© 2025 PatSnap. All rights reserved.Legal|Privacy policy|Modern Slavery Act Transparency Statement|Sitemap|About US| Contact US: help@patsnap.com