Repair material for repairing turbine blade tip cracks and repair method thereof
A technology of turbine blade and repair method, applied in the direction of metal material coating process, coating, etc., can solve the problems of easy precipitation of second phase, large heat-affected zone, inconcentration of argon arc welding energy, etc., and achieves the goal of promoting application development. Effect
- Summary
- Abstract
- Description
- Claims
- Application Information
AI Technical Summary
Problems solved by technology
Method used
Image
Examples
Embodiment 1
[0032] A repairing material for repairing cracks at the tip of turbine blades, which is a high-strength oxidation-resistant nickel-based superalloy powder, consisting of the following components in mass percentage: 8.6% chromium, 15% cobalt, 0.25% carbon, and 2.3% molybdenum , 3.4% tungsten, 6.1% aluminum, 5.4% tantalum, 0.03 zirconium, 0.05% boron, 1.6% rhenium, 1.5% hafnium, and the balance is nickel.
Embodiment 2
[0034] A repairing material for repairing cracks at the tip of turbine blades, which is a high-strength oxidation-resistant nickel-based superalloy powder, composed of the following components in mass percentage: 10% chromium, 13% cobalt, 0.2% carbon, and 2.7% molybdenum , tungsten 4.1%, aluminum 6%, tantalum 6.2%, zirconium 0.05, boron 0.02%, rhenium 2%, hafnium 2.7%, and the balance is nickel.
Embodiment 3
[0036] A repairing material for repairing cracks at the tip of turbine blades, which is a high-strength anti-oxidation nickel-based superalloy powder with a particle size of -100~+325 mesh, composed of the following components in mass percentage: 9% chromium, cobalt 14%, carbon 0.22%, molybdenum 2.5%, tungsten 4%, aluminum 6.2%, tantalum 6%, zirconium 0.04, boron 0.03%, rhenium 1.8%, hafnium 2%, and the balance is nickel.
PUM
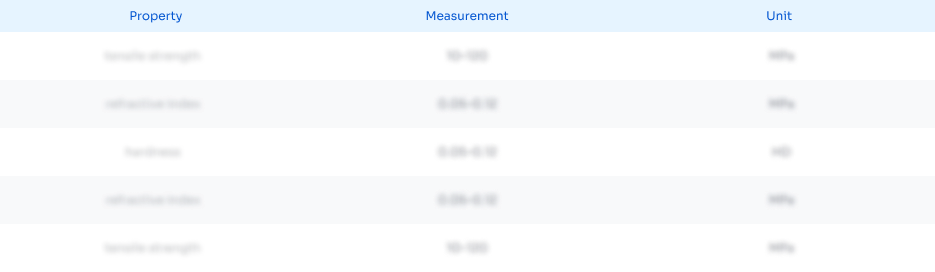
Abstract
Description
Claims
Application Information

- R&D
- Intellectual Property
- Life Sciences
- Materials
- Tech Scout
- Unparalleled Data Quality
- Higher Quality Content
- 60% Fewer Hallucinations
Browse by: Latest US Patents, China's latest patents, Technical Efficacy Thesaurus, Application Domain, Technology Topic, Popular Technical Reports.
© 2025 PatSnap. All rights reserved.Legal|Privacy policy|Modern Slavery Act Transparency Statement|Sitemap|About US| Contact US: help@patsnap.com