Method for preparing benzaldehyde by continuously oxidizing methylbenzene through tubular reactor
A tubular reactor and benzaldehyde technology, applied in the direction of oxidation to prepare carbonyl compounds, etc., can solve the problems of target product selectivity, low yield, low oxidant utilization rate, poor mass transfer and heat transfer effect, etc., to improve the reaction rate And the utilization rate of raw materials, avoiding the use of co-catalysts, and expanding the effect of production scale
- Summary
- Abstract
- Description
- Claims
- Application Information
AI Technical Summary
Problems solved by technology
Method used
Image
Examples
Embodiment 1
[0032] (1) Device: refer to figure 2 Determine the connection mode of the tubular reactor. The pipeline type is: (3a+3b) direct flow channel + round cake pulse variable diameter rectangular flat pipeline. The inner diameter and volume of the pipeline are determined according to the flow rate and reaction residence time. The heat exchange medium is heat conduction Oil.
[0033] (2) Dissolve 6.06g of cobalt acetate and 6.06g of sodium molybdate in 200ml of toluene and 200ml of acetic acid to form a mixed solution. At this time, n (cobalt acetate): n (toluene) = 0.015:1, and dissolve 6.06g of sodium bromide at 15%H 2 o 2 form H 2 o 2 -Acetic acid solution, at this time n (sodium bromide):n (toluene)=0.015:1, toluene-acetic acid solution and H 2 o 2 -Acetic acid solution is injected in the tubular reactor of continuous heat exchange by constant flow pump respectively with the flow velocity of 8.33ml / min and 16.67ml / min, at this moment n (H 2 o 2 ): n (toluene) = 2:1, usin...
Embodiment 2
[0035] (1) Device: refer to figure 2 Determine the connection mode of the tubular reactor. The pipeline type is: (3a+3c) direct flow channel + oblique square cake pulse variable diameter rectangular flat pipeline. The inner diameter and volume of the pipeline are determined according to the flow rate and reaction residence time. The heat exchange medium is heat transfer oil.
[0036] (2) Dissolve 12.12g of cobalt acetate and 12.12g of sodium molybdate in 200ml of toluene and 200ml of acetic acid to form a mixed solution. At this time, n (cobalt acetate): n (toluene) = 0.03:1, and dissolve 12.12g of sodium bromide at 15%H 2 o 2 form H 2 o 2 -Acetic acid solution, at this time n (sodium bromide):n (toluene)=0.03:1, toluene-acetic acid solution and H 2 o 2 -Acetic acid solution is injected in the tubular reactor of continuous heat exchange by constant flow pump respectively with the flow velocity of 8.33ml / min and 16.67ml / min, at this moment n (H 2 o 2 ): n (toluene) = 2...
Embodiment 3
[0038] (1) Device: refer to figure 2 Determine the connection mode of the tubular reactor. The pipeline type is: (3a+3d) straight-through channel + enhanced mixing circular cake type rectangular flat pipeline. The inner diameter and volume of the pipeline are determined according to the flow rate and reaction residence time, and the heat transfer medium is heat transfer oil. .
[0039] (2) Dissolve 6.06g of cobalt acetate and 6.06g of sodium molybdate in 200ml of toluene and 200ml of acetic acid to form a mixed solution. At this time, n (cobalt acetate): n (toluene) = 0.015:1, and dissolve 6.06g of sodium bromide at 15%H 2 o 2 form H 2 o 2 -Acetic acid solution, at this time n (sodium bromide):n (toluene)=0.015:1, toluene-acetic acid solution and H 2 o 2 -Acetic acid solution is injected in the tubular reactor of continuous heat exchange by constant flow pump respectively with the flow velocity of 8.33ml / min and 16.67ml / min, at this moment n (H 2 o 2 ): n (toluene) = ...
PUM
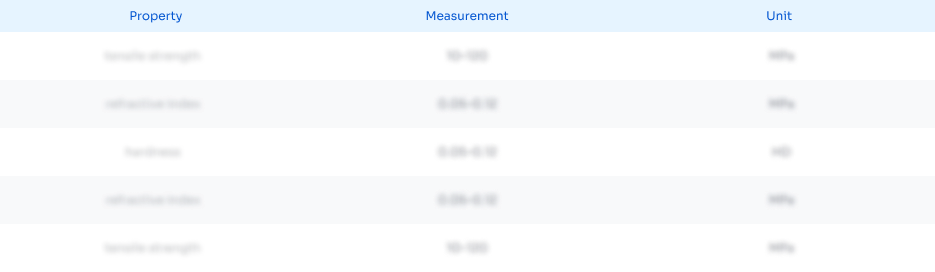
Abstract
Description
Claims
Application Information

- R&D
- Intellectual Property
- Life Sciences
- Materials
- Tech Scout
- Unparalleled Data Quality
- Higher Quality Content
- 60% Fewer Hallucinations
Browse by: Latest US Patents, China's latest patents, Technical Efficacy Thesaurus, Application Domain, Technology Topic, Popular Technical Reports.
© 2025 PatSnap. All rights reserved.Legal|Privacy policy|Modern Slavery Act Transparency Statement|Sitemap|About US| Contact US: help@patsnap.com