Preparation method for electronic substrate welding assistant
A technology of welding aids and electronic substrates, which is applied in the direction of welding equipment, welding media, welding/cutting media/materials, etc., can solve the problems of electronic substrate electrical insulation performance decline, environmental pollution reduction, surface activity increase, etc., to achieve no need Cleansing, less residue, anti-oxidation effect
- Summary
- Abstract
- Description
- Claims
- Application Information
AI Technical Summary
Problems solved by technology
Method used
Examples
example 1
[0016] First weigh 1mL succinic acid, 1mL oxalic acid, 0.2mL triethanolamine, add 20mL deionized water, stir at 300r / min and heat to 50°C, add 10mL acrylic resin A890, heat up to 90°C, continue stirring for 3h, Cool to room temperature, then filter, put the filter residue in a drying oven, dry to constant weight at 105°C, then add it to a pulverizer to pulverize, pass through a 200-mesh sieve, and obtain a microencapsulated compound active substance, which is ready for use; Take 400g of masson pine rosin, put it into a four-necked flask, raise the temperature to 180°C under a nitrogen atmosphere, add 120g of maleic anhydride, keep the temperature for 3 hours, then pour it into 1.5L of turpentine at a temperature of 50°C, at 300r / min Stir and heat until the solid is completely dissolved, stop heating and let it stand for 10 hours, then filter it with suction, place the filter cake in a vacuum drying oven, and dry it at 120°C to constant weight to obtain maleopimaric anhydride; w...
example 2
[0019] First weigh 2mL succinic acid, 2mL oxalic acid, 0.4mL triethanolamine, add 30mL deionized water, stir at 400r / min and heat to 60°C, add 12mL acrylic resin A890, heat up to 95°C, continue stirring for 4h, Cool to room temperature, then filter, put the filter residue in a drying oven, dry to constant weight at 110°C, put it into a pulverizer and grind it, pass through a 200-mesh sieve to obtain a microencapsulated compound active substance, which is ready for use; Take 450g of masson pine rosin, put it into a four-necked flask, raise the temperature to 200°C under a nitrogen atmosphere, add 136g of maleic anhydride, keep the temperature for 4 hours, then pour it into 2.1L of turpentine at a temperature of 60°C, at 400r / min Stir and heat until the solid is completely dissolved, stop heating and let it stand for 12 hours, then filter with suction, place the filter cake in a vacuum drying oven, and dry it to constant weight at 125°C to obtain maleopimaric anhydride; weigh 60g...
example 3
[0022] First weigh 1.5mL succinic acid, 1.5mL oxalic acid, 0.3mL triethanolamine, add 25mL deionized water, stir at 350r / min and heat to 55°C, add 11mL acrylic resin A890, heat up to 93°C, continue stirring 3.5h, cooled to room temperature, and then filtered, the filter residue was placed in a drying oven, dried at 110°C to constant weight, then added to a pulverizer for pulverization, and passed through a 200-mesh sieve to obtain a microencapsulated compound active substance. Standby; weigh 450g of masson pine rosin, put it into a four-necked flask, heat up to 190°C under a nitrogen atmosphere, add 128g of maleic anhydride, keep the temperature for 3.5 hours, then pour into 1.9L of turpentine at a temperature of 55°C, Stir at 350r / min and heat until the solid is completely dissolved, stop heating and let it stand for 11h, then filter with suction, place the filter cake in a vacuum drying oven, and dry at 125°C to constant weight to obtain maleopimaric anhydride; weigh 55g Add...
PUM
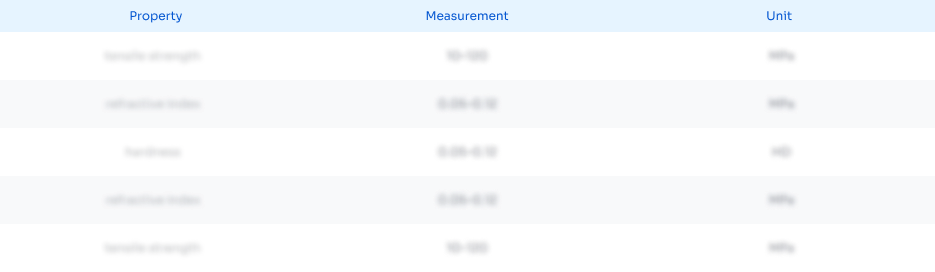
Abstract
Description
Claims
Application Information

- R&D Engineer
- R&D Manager
- IP Professional
- Industry Leading Data Capabilities
- Powerful AI technology
- Patent DNA Extraction
Browse by: Latest US Patents, China's latest patents, Technical Efficacy Thesaurus, Application Domain, Technology Topic, Popular Technical Reports.
© 2024 PatSnap. All rights reserved.Legal|Privacy policy|Modern Slavery Act Transparency Statement|Sitemap|About US| Contact US: help@patsnap.com