Laser welding method for titanium alloy blade
A welding method and technology of titanium alloy, applied in laser welding equipment, welding equipment, welding/welding/cutting objects, etc., can solve the problems of lowering yield, surface collapse, shrinkage porosity, etc., to improve connection strength, avoid Stress concentration, effect of improving welding quality
- Summary
- Abstract
- Description
- Claims
- Application Information
AI Technical Summary
Problems solved by technology
Method used
Examples
Embodiment 1
[0011] 1) Process grooves at the joints of the blade, the blade body and the base. The grooves are Y-shaped grooves with a blunt edge gap of 2 mm. T-shaped interlocking parts are processed on both sides of the grooves. The T-shaped component includes a first end and a second end, the width of the first end is 2mm, and the width of the second end is 1.3mm, and the connection between the first end and the second end adopts a round corner transition, and the The T-shaped parts are alternately distributed on both sides of the groove, with an interval of 5mm, and form an interlocking structure during welding. It is carried out by using YAG laser or CO2 laser plus electric arc as the composite heat source, and the method of cold metal transition. The first layer The laser power used is 10KW, the current is 220A, the welding speed is 0.8m / min, the wire feeding speed is 70ipm; the laser defocus is 5mm, the laser power used for the second layer welding is 8KW, the current is 280A, and t...
Embodiment 2
[0013] A laser arc composite heat source cold metal transition welding method for a titanium alloy blade is characterized in that it comprises the following steps:
[0014] 1) Process grooves at the joints of the blade, the blade body and the base. The grooves are Y-shaped grooves with a blunt edge clearance of 2.5 mm. T-shaped interlocking parts are processed on the slopes on both sides of the grooves. , the T-shaped component includes a first end and a second end, the width of the first end is 2-2.5mm, the width of the second end is 1mm, and the connection between the first end and the second end adopts a round transition, The T-shaped components are alternately distributed on both sides of the groove, with a spacing of 5 mm, and form an interlocking structure during welding.
[0015] 2) Welding process, using laser plus arc as composite heat source, cold metal transition, double-layer single-channel method, the laser power used in the first layer is 10KW, the current is 220...
PUM
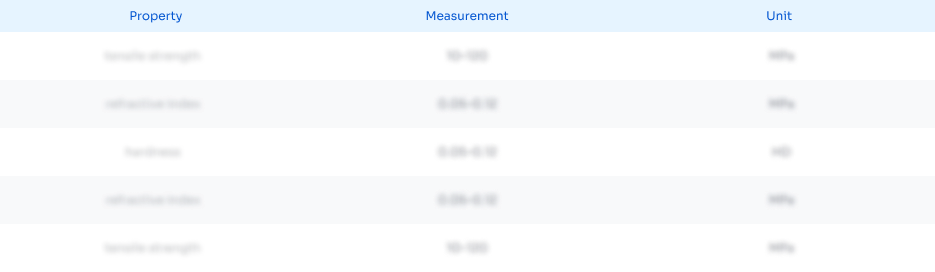
Abstract
Description
Claims
Application Information

- R&D Engineer
- R&D Manager
- IP Professional
- Industry Leading Data Capabilities
- Powerful AI technology
- Patent DNA Extraction
Browse by: Latest US Patents, China's latest patents, Technical Efficacy Thesaurus, Application Domain, Technology Topic, Popular Technical Reports.
© 2024 PatSnap. All rights reserved.Legal|Privacy policy|Modern Slavery Act Transparency Statement|Sitemap|About US| Contact US: help@patsnap.com