Manganese zinc ferrite material with wide temperature and low power as well as preparation method thereof
A ferrite material, power consumption manganese-zinc technology, applied in the direction of magnetic materials, inorganic material magnetism, magnetic objects, etc., can solve the problems of lack of regulation, lack of loss information, etc., to reduce hysteresis loss and eddy current loss, reduce Eddy current loss, effect of increasing saturation magnetic flux density
- Summary
- Abstract
- Description
- Claims
- Application Information
AI Technical Summary
Problems solved by technology
Method used
Image
Examples
Embodiment 1
[0031] Embodiment 1: take main component raw material by weighing following main component content: Fe 2 o 3 The content is 53.1mol%, the ZnO content is 9.2mol%, and the MnO content is 37.7mol%. It is pre-calcined after sand-milling and spray-drying. The pre-calcination temperature is 900°C and the time is 120 minutes. Add the auxiliary component raw materials weighed in proportion to the calcined material. The content of auxiliary components based on the total weight of the main components is: CaCO 3 : 0.04%, Nb 2 o 5 : 0.03%, Co 2 o 3 : 0.4%, SnO 2 : 0.1%, NaHCO 3 : 0.02%, carry out sand grinding, the time is 120 minutes, and the average grain size of the sand abrasive is 0.9 μm. Then spray granulate the sand abrasive, and press the H25 / 15 / 10 ring sample with a molding machine.
Embodiment 2
[0037] Embodiment 2: take main component raw material by weighing following main component content: Fe 2 o 3 content of 53.1mol%, ZnO content of 9.2mol%, MnO content of 37.7mol%, pre-calcined after sand milling and spray drying, the pre-calcination temperature is 900 ℃, the time is 120 minutes; The proportion of auxiliary component raw materials taken by weight, the content of auxiliary components by the total weight of the main component is CaCO 3 : 0.04%, Nb 2 o 5 : 0.03%, Co 2 o 3 : 0.4%, SnO 2 : 0.1%, NaHCO 3 : 0.02%, carry out sand grinding, the time is 120 minutes, and the average grain size of the sand abrasive is 0.9 μm. Then spray granulate the sand abrasive, and press the H25 / 15 / 10 ring sample with a molding machine.
Embodiment 3
[0046] Embodiment 3: take main component raw material by weighing following main component content: Fe 2 o 3 content of 53.1mol%, ZnO content of 9.2mol%, MnO content of 37.7mol%, pre-calcined after sand milling and spray drying, the pre-calcination temperature is 900 ℃, the time is 120 minutes; The auxiliary component raw material that the ratio takes (the auxiliary component content by main component gross weight is: CaCO 3 : 0.04%, Nb 2 o 5 : 0.03%, Co 2 o 3 : 0.4%, SnO 2 : 0.1%, NaHCO 3 : 0.02%, carry out sand grinding, the time is 120 minutes, and the average grain size of the sand abrasive is 0.9 μm. Then carry out spray granulation on this abrasive material, press the H25 / 15 / 10 ring sample with a molding machine, sinter and keep it warm for 60 minutes when the temperature is lowered to 1200°C.
PUM
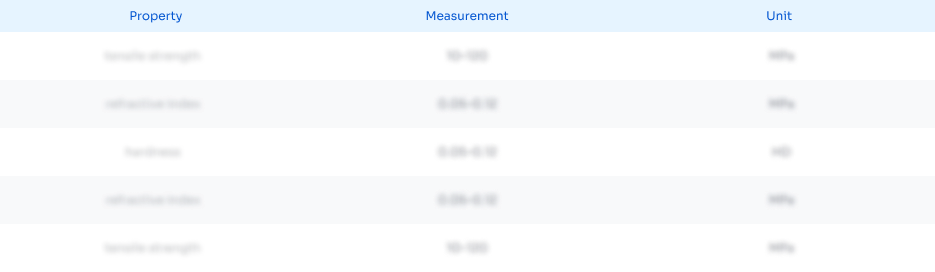
Abstract
Description
Claims
Application Information

- R&D Engineer
- R&D Manager
- IP Professional
- Industry Leading Data Capabilities
- Powerful AI technology
- Patent DNA Extraction
Browse by: Latest US Patents, China's latest patents, Technical Efficacy Thesaurus, Application Domain, Technology Topic, Popular Technical Reports.
© 2024 PatSnap. All rights reserved.Legal|Privacy policy|Modern Slavery Act Transparency Statement|Sitemap|About US| Contact US: help@patsnap.com