Two-component low-toxicity flame-retardant epoxy-based joint mixture and preparation method thereof
An epoxy-based, two-component technology, applied in the field of coatings, can solve the problem that it is not suitable for ships, does not have low toxicity, flame retardant, seawater corrosion resistance, self-leveling, smoke suppression, and does not meet the requirements of marine caulking agents, etc. problems, to achieve good self-leveling characteristics, improve the flame retardant effect, and reduce the amount of addition.
- Summary
- Abstract
- Description
- Claims
- Application Information
AI Technical Summary
Problems solved by technology
Method used
Image
Examples
preparation example Construction
[0025] The preparation method of the two-component epoxy-based flame-retardant low-toxicity caulking agent of the present invention, the detailed steps are as follows:
[0026] (1) According to the ratio of the raw materials of the aforementioned caulking agent, weigh each raw material and set aside;
[0027] (2) Preparation of resin component A: Mix hydroxide compound, acid zinc compound, high wear-resistant carbon black and precipitated silica in a powder disperser, and the stirring blade rotates at 100-150r / min, and disperses Treat for 15-20 minutes to form a powder mixture; stir and mix the phosphating epoxy resin and silicone coupling agent in a double planetary mixer, the stirring speed is 40-60r / min, and the mixing time is 40-60min; the powder Put the mixture into the mixer, soak it for 10-12 hours and then stir it. The speed of the stirring blade is 100-120r / min, and the mixing time is 60-80min. Grind repeatedly on the grinder until the fineness is less than 50 μm, an...
Embodiment 1
[0031] Preparation of resin component A: In parts by weight, weigh 40 parts of magnesium hydroxide, 60 parts of zinc borate, 2 parts of high wear-resistant carbon black, and 10 parts of precipitated white carbon black, and put them into a powder disperser for mixing , stirring paddle speed 150r / min, dispersion treatment 20min, forming a powder mixture; stirring and mixing 100 parts of phosphating epoxy resin and 5 parts of anilinomethyltrimethoxysilane in a double planetary mixer, stirring speed 60r / min, mixing time 60min; put the powder mixture into the mixer, soak for 12h and then stir, the speed of the stirring paddle is 120r / min, and the mixing time is 80min; Grind to a fineness of 46 μm, and pack into barrels to obtain resin component A.
[0032] Preparation of curing agent component B: in parts by weight, weigh 40 parts of phenalkamine T31 and 10 parts of DMP-30 respectively, stir and mix in a double planetary mixer, the speed of the stirring blade is 60r / min, the mixing...
Embodiment 2
[0035] Preparation of resin component A: In parts by weight, weigh 60 parts of aluminum hydroxide, 40 parts of zinc stannate, 1 part of high wear-resistant carbon black, and 15 parts of precipitated white carbon black, and put them into a powder disperser for Mixing, stirring paddle speed 100r / min, dispersing treatment for 15min, forming a powder mixture; stirring and mixing 100 parts of phosphating epoxy resin and 3 parts of γ-aminopropyltriethoxysilane in a double planetary mixer, The speed of the stirring blade is 40r / min, and the mixing time is 50min; put the powder mixture into the mixer, soak for 10h and then stir, the speed of the stirring blade is 100r / min, and the mixing time is 60min; after stirring evenly, add the stirring material to the three-roll grinding Grind in the machine until the fineness is 48 μm, and put into barrels to obtain resin component A.
[0036]Preparation of curing agent component B: in parts by weight, weigh 50 parts of polyamide 651 and 8 part...
PUM
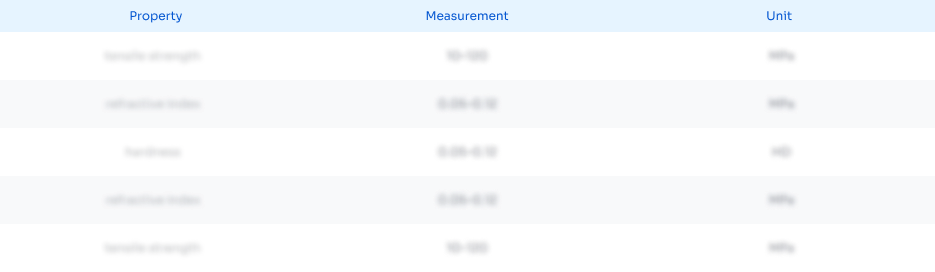
Abstract
Description
Claims
Application Information

- R&D
- Intellectual Property
- Life Sciences
- Materials
- Tech Scout
- Unparalleled Data Quality
- Higher Quality Content
- 60% Fewer Hallucinations
Browse by: Latest US Patents, China's latest patents, Technical Efficacy Thesaurus, Application Domain, Technology Topic, Popular Technical Reports.
© 2025 PatSnap. All rights reserved.Legal|Privacy policy|Modern Slavery Act Transparency Statement|Sitemap|About US| Contact US: help@patsnap.com