High-nitrogen steel pressure welding device and method for welding high-nitrogen steel by using same
A technology of pressure welding and high nitrogen steel, applied in the direction of auxiliary devices, welding media, welding equipment, etc., can solve the problems of inconspicuous effect, difficulty in overcoming the loss of nitrogen element, etc., achieve reasonable composition, improve mechanical properties, weld good seam quality
- Summary
- Abstract
- Description
- Claims
- Application Information
AI Technical Summary
Problems solved by technology
Method used
Image
Examples
Embodiment 1
[0033] See attached figure 1 , a high-nitrogen steel pressurized welding device, comprising a closed welding chamber 1, a gas mixing chamber 2, a vacuum pump 3; Valves 4 and 5 are respectively set on the gas pipeline and the gas pipeline connecting the airtight welding room and the vacuum pump; the airtight welding room is equipped with a support 6, a welding power supply 7, a welding wire rack 8, and a wire feeding mechanism 9; a trolley 10 is set on the support; a welding wire rack It is installed on the trolley with the wire feeding mechanism; a cooling plate 11 is arranged above the bracket; a welding wire sleeve 12 is connected under the wire feeding mechanism; a welding gun 13 is connected to the end of the welding wire sleeve; the welding power supply is connected to the welding wire sleeve, The bracket is connected; the cooling plate is a water-cooled copper plate, and the circulating water circuit is set inside as a cold source, and the water body inlet and outlet are...
Embodiment 2
[0035] A device for pressurized welding of high-nitrogen steel, comprising an airtight welding chamber, a gas mixing chamber, and a vacuum pump; the airtight welding chamber communicates with the gas mixing chamber and the vacuum pump through gas pipes, and the air pipe connecting the airtight welding chamber and the gas mixing chamber and The airtight welding chamber and the vacuum pump are respectively provided with valves on the gas pipelines; the airtight welding chamber is equipped with a support, welding power supply, welding wire rack, and wire feeding mechanism; a trolley is set on the bracket; There is a cooling plate; the welding wire sleeve is connected under the wire feeding mechanism; the welding torch is connected to the end of the welding wire sleeve; the welding power supply is connected to the welding wire sleeve and the bracket through the electrode wire respectively; the cooling plate is a water-cooled copper plate, and a circulating water circuit is set insid...
Embodiment 3
[0037] A device for pressurized welding of high-nitrogen steel, comprising an airtight welding chamber, a gas mixing chamber, and a vacuum pump; the airtight welding chamber communicates with the gas mixing chamber and the vacuum pump through gas pipes, and the air pipe connecting the airtight welding chamber and the gas mixing chamber and The airtight welding chamber and the vacuum pump are respectively provided with valves on the gas pipelines; the airtight welding chamber is equipped with a support, welding power supply, welding wire rack, and wire feeding mechanism; a trolley is set on the bracket; There is a cooling plate; a welding wire sleeve is connected under the wire feeding mechanism; a welding torch is connected to the end of the welding wire sleeve; the welding power supply is respectively connected to the welding wire sleeve and the bracket through the electrode wire; the cooling plate is a hollow copper plate, and a dry ice block is installed inside to source; th...
PUM
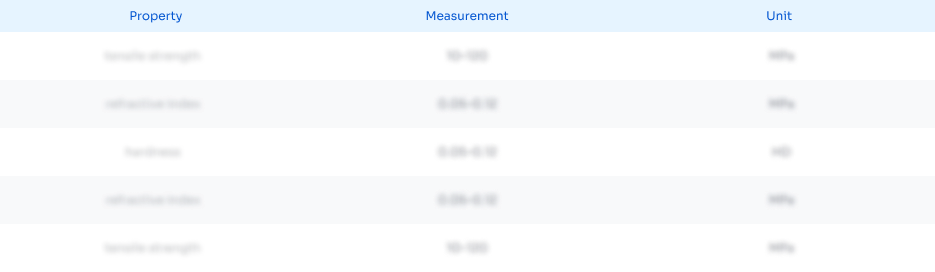
Abstract
Description
Claims
Application Information

- R&D
- Intellectual Property
- Life Sciences
- Materials
- Tech Scout
- Unparalleled Data Quality
- Higher Quality Content
- 60% Fewer Hallucinations
Browse by: Latest US Patents, China's latest patents, Technical Efficacy Thesaurus, Application Domain, Technology Topic, Popular Technical Reports.
© 2025 PatSnap. All rights reserved.Legal|Privacy policy|Modern Slavery Act Transparency Statement|Sitemap|About US| Contact US: help@patsnap.com