Recycling method of alkali fusion solution of 1-amino-8-naphthol-3,6-disulfonic acid
A technology of resource utilization and molten solution, which is applied in the field of resource utilization of H acid-base molten solution, can solve the problems of serious environmental pollution, difficult treatment, consumption of sulfuric acid, etc., and achieve the effects of reducing emissions, reducing consumption and saving costs
- Summary
- Abstract
- Description
- Claims
- Application Information
AI Technical Summary
Problems solved by technology
Method used
Image
Examples
Embodiment 1
[0020] Add 99% dichloropropanol 199g (1.527mol) in the 1000ml reactor, with negative pressure-0.085MPa, stir and heat up to 60°C, start to drop 500g of H acid-base solution, free alkali content 11% (converted to NaOH1. 375mol), H acid content 13.8%, dropwise addition time 90min, dropwise process keep kettle temperature 60 ~ 62 ℃, dropwise end, continue distillation 5min; The oil layer is 130.76g, and the gas spectrum analysis contains ECH85.26%, DCH13.23%, and the water separation layer is 201g, and the gas spectrum analysis contains ECH5.6%, DCH1.15%. Yield 96.5% (based on converted DCH).
Embodiment 2
[0022] Add 99% dichloropropanol 376.3g (2.888mol) in 1000ml reactor, bring negative pressure-0.095MPa, stir and heat up to 50 ℃, begin to dropwise add H acid-base solution 350g, free alkali content 16.5% (reduce NaOH1 .444mol), H acid content 13.8%, drop time 90min, dropwise process keep kettle temperature 49~52 ℃, dropwise finish, continue distillation 5min; Analysis; oil layer 368.9g, gas spectrum analysis contains ECH32.4%, DCH48.99%, water separation layer 175.5g, gas spectrum analysis contains ECH6.1%, DCH3.15%, according to the analysis calculation DCH conversion rate is 50%, ECH yield 97.5% (based on converted DCH).
Embodiment 3
[0024] Add 268.4g (2.06mol) of 99% dichloropropanol in a 1000ml reactor, stir and heat up to 45°C, start to add 350g of H acid-base solution dropwise, the free alkali content is 20% (NaOH1.75mol), and the H acid content 20%, adding time for 10 minutes, keep the temperature of the kettle at 45-50°C during the dropping process, continue to keep warm for 10 minutes after the dropping is completed; cool down the feed liquid, let it stand for 10 minutes, pour the clear liquid into the separatory funnel to separate layers, and separate the oil layer ①189. 3g, the brine layer was divided into the reaction kettle, stripped with negative pressure -0.09MPa until no oil drops were distilled, the distillate was poured into the separatory funnel to separate layers, the oil separation layer ② 6.93g, the water separation layer 97.5g, gas spectrometry analysis Contains 3.56% ECH and 1.98% DCH, combined two oil layer gas spectrometry analysis contains 79.1% ECH, 19.4% DCH; saponification kettle...
PUM
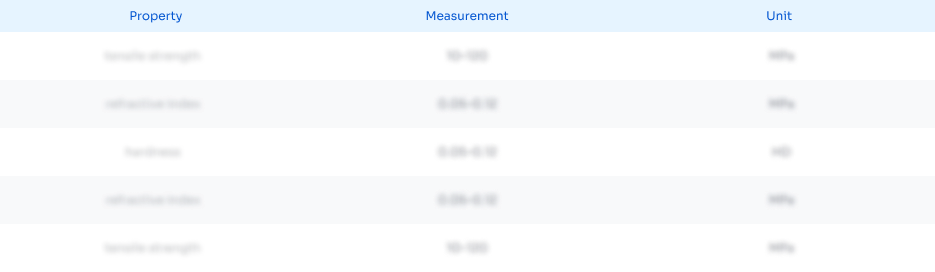
Abstract
Description
Claims
Application Information

- R&D Engineer
- R&D Manager
- IP Professional
- Industry Leading Data Capabilities
- Powerful AI technology
- Patent DNA Extraction
Browse by: Latest US Patents, China's latest patents, Technical Efficacy Thesaurus, Application Domain, Technology Topic, Popular Technical Reports.
© 2024 PatSnap. All rights reserved.Legal|Privacy policy|Modern Slavery Act Transparency Statement|Sitemap|About US| Contact US: help@patsnap.com