Selective welding carrier and welding method thereof
A welding method and carrier technology, which is applied in the direction of assembling printed circuits with electrical components, can solve the problems of interference from other devices, increased production management costs, and failure to complete, so as to reduce the frequency of loading and unloading, and the judgment standard is simple and clear , the effect of improving production efficiency
- Summary
- Abstract
- Description
- Claims
- Application Information
AI Technical Summary
Problems solved by technology
Method used
Image
Examples
Embodiment 1
[0051] Follow the steps in turn:
[0052] Step 1. Adjust the state of the selective welding machine and welding parameters, and put the welding plate into the selective welding machine; the welding parameters are:
[0053] The amount of flux sprayed is 90%;
[0054] The pre-heating stage is divided into three stages; the first stage preheating time is 20S, and the preheating power is 60% of the total power; the second stage is 20S, and the preheating power is 75% of the total power; the third stage The stage preheating time is 20S, and the preheating power is 90% of the total power.
[0055] The preheating time for the difficult point of tin penetration is 20S; the height between the welding nozzle and the board surface is 6.5mm;
[0056] The hot air preheating temperature setting temperature is 160°C (the actual board surface temperature is about 120°C);
[0057] The hot air preheating time is consistent with the welding time; the welding time is 2S; the welding temperatur...
Embodiment 2
[0065] The welding temperature in the welding parameters in Example 1 was reduced to 285° C., and other parameters and steps remained unchanged.
[0066] Experiments have proved that under this welding parameter, the requirement of 100% penetration of tin in all solder joints can be achieved. In conclusion, when other welding parameters remain unchanged, the welding temperature can be appropriately reduced.
Embodiment 3
[0068] The soldering temperature in the soldering parameters in Example 1 is reduced to 285°C, the preheating time at the point where tin penetration is difficult is reduced to 10S, and other parameters and steps remain unchanged.
[0069] Experiments have proved that under this welding parameter, the requirement of 100% penetration of tin in all solder joints can be achieved.
[0070] In conclusion, when other welding parameters remain unchanged, the preheating time of the welding head can be appropriately shortened.
PUM
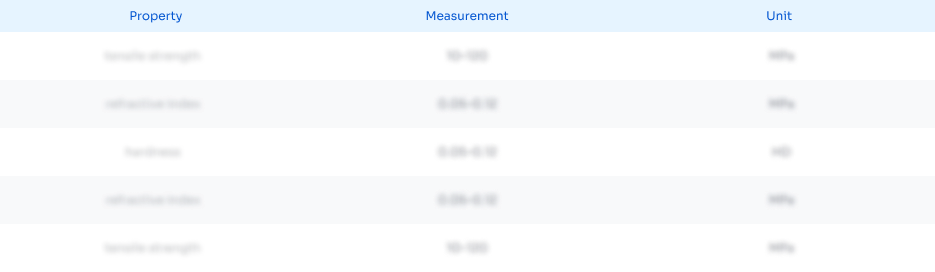
Abstract
Description
Claims
Application Information

- R&D Engineer
- R&D Manager
- IP Professional
- Industry Leading Data Capabilities
- Powerful AI technology
- Patent DNA Extraction
Browse by: Latest US Patents, China's latest patents, Technical Efficacy Thesaurus, Application Domain, Technology Topic, Popular Technical Reports.
© 2024 PatSnap. All rights reserved.Legal|Privacy policy|Modern Slavery Act Transparency Statement|Sitemap|About US| Contact US: help@patsnap.com