Plant fiber-reinforced composite plastic
A technology of reinforced composite and plant fiber, which is applied in the field of materials, can solve the problems of poor mechanical strength, etc., and achieve the effects of high tensile strength and impact strength, stable size and low cost
- Summary
- Abstract
- Description
- Claims
- Application Information
AI Technical Summary
Problems solved by technology
Method used
Examples
Embodiment 1
[0015] A plant fiber reinforced composite plastic, comprising the following raw material components in parts by weight: 50 parts of polyvinyl chloride resin, 40 parts of pineapple leaf fiber base, 8 parts of calcium carbonate, 10 parts of carboxyethyl cellulose, nano-montmorillonite 7 parts, 35 parts of basalt fiber, 60 parts of wood fiber, 3.5 parts of methylisothiazolinone, 2 parts of camphor wood powder, 2 parts of thorny aralia powder, 0.1 part of agarwood powder, 9 parts of melamine cyanurate, carbonized 8 parts of silicon powder, 14 parts of sodium carboxymethyl cellulose, 3 parts of sepiolite, 10 parts of asbestos powder, 13 parts of acetyl tributyl citrate, 2 parts of diethylene glycol monoethyl ether acetate, magnesium stearate 1 part, 4 parts of 3-hydroxybenzoic acid, 4 parts of diethylenetriamine, 0.2 part of palladium nitrate, 0.2 part of diyttrium trioxide, 2 parts of gelatin.
[0016] The preparation method of the present invention is the same as the prior art. ...
Embodiment 2
[0018] A plant fiber reinforced composite plastic, comprising the following raw material components in parts by weight: 60 parts of polyvinyl chloride resin, 65 parts of pineapple leaf fiber base, 15 parts of calcium carbonate, 20 parts of carboxyethyl cellulose, nano-montmorillonite 9 parts, 45 parts of basalt fiber, 65 parts of wood fiber, 4.5 parts of methylisothiazolinone, 4 parts of camphor wood powder, 4 parts of thorny aralia powder, 0.2 parts of agarwood powder, 13 parts of melamine cyanurate, carbonized 10 parts of silicon powder, 20 parts of sodium carboxymethyl cellulose, 7 parts of sepiolite, 20 parts of asbestos powder, 15 parts of acetyl tributyl citrate, 3 parts of diethylene glycol monoethyl ether acetate, magnesium stearate 2 parts, 6 parts of 3-hydroxybenzoic acid, 6 parts of diethylenetriamine, 0.4 parts of palladium nitrate, 0.4 parts of diyttrium trioxide, and 3 parts of gelatin.
[0019] The preparation method of the present invention is the same as the p...
Embodiment 3
[0021] A plant fiber reinforced composite plastic, comprising the following raw material components in parts by weight: 55 parts of polyvinyl chloride resin, 50 parts of pineapple leaf fiber base, 10 parts of calcium carbonate, 15 parts of carboxyethyl cellulose, nano-montmorillonite 8 parts, 35 parts of basalt fiber, 60 parts of wood fiber, 4 parts of methylisothiazolinone, 3 parts of camphor wood powder, 3 parts of thorny aralia powder, 0.2 parts of agarwood powder, 12 parts of melamine cyanurate, carbonized 9 parts of silicon powder, 15 parts of sodium carboxymethyl cellulose, 4 parts of sepiolite, 15 parts of asbestos powder, 14 parts of acetyl tributyl citrate, 2 parts of diethylene glycol monoethyl ether acetate, magnesium stearate 1 part, 5 parts of 3-hydroxybenzoic acid, 5 parts of diethylenetriamine, 0.4 parts of palladium nitrate, 0.4 parts of diyttrium trioxide, and 3 parts of gelatin.
PUM
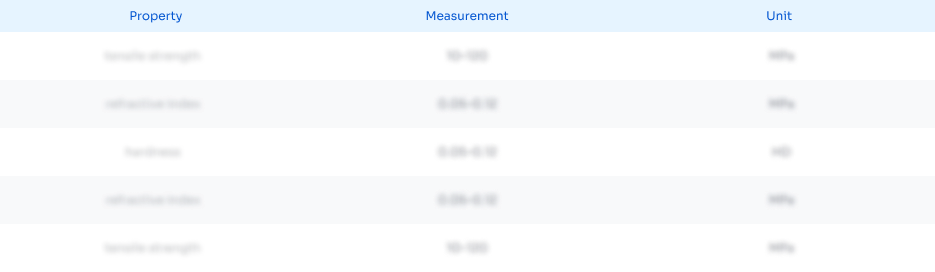
Abstract
Description
Claims
Application Information

- Generate Ideas
- Intellectual Property
- Life Sciences
- Materials
- Tech Scout
- Unparalleled Data Quality
- Higher Quality Content
- 60% Fewer Hallucinations
Browse by: Latest US Patents, China's latest patents, Technical Efficacy Thesaurus, Application Domain, Technology Topic, Popular Technical Reports.
© 2025 PatSnap. All rights reserved.Legal|Privacy policy|Modern Slavery Act Transparency Statement|Sitemap|About US| Contact US: help@patsnap.com