Epoxy resin seepy material and preparation method thereof and application
A technology of epoxy resin and water-permeable material, applied in application, other household appliances, household appliances, etc., can solve the problems of complicated operation and high-temperature curing, and achieve the effect of uniform pore distribution, excellent water permeability and air permeability, and uniform pore size distribution.
- Summary
- Abstract
- Description
- Claims
- Application Information
AI Technical Summary
Problems solved by technology
Method used
Image
Examples
Embodiment 1
[0043] At a room temperature of 35°C, 64.8g of water, 51.84g of silicon micropowder, 9.72g of aluminum oxide powder, 1.12g of boron oxide, and 1.12g of zinc oxide (the average particle size of the filler is 1250 mesh) were added to the container and mixed uniformly to obtain Water phase component; Add 101.6g epoxy resin, 60.47g epoxy resin curing agent, 10.68g butyl glycidyl ether, 10.04g polyether amine T403, 10g containing polyoxypropylene segment in another container, 3,6-tris(dimethylaminomethyl)phenol was mixed and stirred evenly into the oil phase components at 35°C; then all the water phase components were transferred to the oil phase components under rapid stirring conditions, and stirred After uniformity, the mixed slurry is obtained, and the mixed slurry is quickly transferred to an impermeable plastic mold, left to cure at room temperature 35°C for 12 hours, demoulded after curing, and tested for water permeability, air permeability, water absorption, porosity, aper...
Embodiment 2
[0045] Add 136.9g of water, 123.24g of calcined kaolin, 41.08g of aluminum oxide powder, 20.54g of zinc oxide, 30.81g of boron oxide, and 10.27g of magnesium oxide (the average particle size of the filler is 800 mesh) into the container at room temperature of 25°C Mix well to obtain the water phase components; add 100.04g epoxy resin, 60.68g epoxy resin curing agent, 10.16g trimethylol triglycidyl ether, 10.01g polyoxypropylene chain segment-containing poly Etheramine D230, 10.24g of dimethylaniline was mixed and stirred evenly into the oil phase components at 25°C; then all the water phase components were transferred to the oil phase components under rapid stirring conditions, and after stirring evenly, we obtained Mix the slurry, quickly transfer the mixed slurry to an impermeable plastic mold, let it stand at room temperature 25°C for 24 hours, and demould after curing, and test the water permeability, air permeability, water absorption, porosity, and pore size according to ...
Embodiment 3
[0047] Add 164.6g of water, 148.08g of silicon micropowder, 74.04g of boron oxide, 14.81g of lead oxide, 9.87g of zinc oxide (the average particle size of the filler is 600 mesh) into the container and mix evenly at room temperature at 15°C to obtain the water phase component In another container, add 83.67g epoxy resin, 50.56g epoxy resin curing agent, 18.02g butyl glycidyl ether, 9.04g polyetheramine T403 containing polyoxypropylene chain segment, 7.51g 2,3,6 - Tris(dimethylaminomethyl)phenol was mixed and stirred evenly into the oil phase components at 15°C; then all the water phase components were transferred to the oil phase components under rapid stirring conditions, and after stirring evenly, the obtained Mix the slurry, quickly transfer the mixed slurry to an impermeable plastic mold, let it stand at room temperature at 15°C for 36 hours, remove the mold after curing, and test the water permeability, water absorption rate, porosity, and pore size according to the corres...
PUM
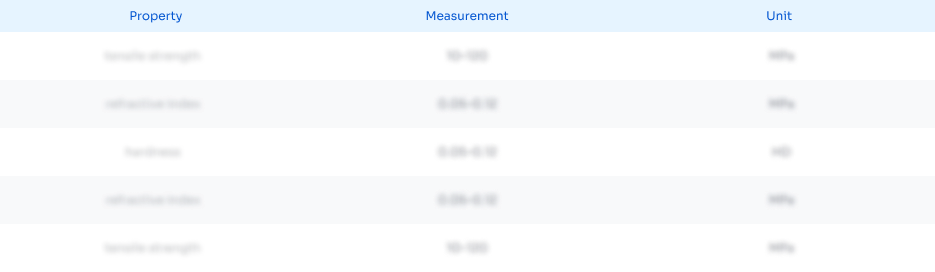
Abstract
Description
Claims
Application Information

- R&D
- Intellectual Property
- Life Sciences
- Materials
- Tech Scout
- Unparalleled Data Quality
- Higher Quality Content
- 60% Fewer Hallucinations
Browse by: Latest US Patents, China's latest patents, Technical Efficacy Thesaurus, Application Domain, Technology Topic, Popular Technical Reports.
© 2025 PatSnap. All rights reserved.Legal|Privacy policy|Modern Slavery Act Transparency Statement|Sitemap|About US| Contact US: help@patsnap.com