Manufacturing method of enhanced type flame-retardant anti-aging polyester film
A manufacturing method and anti-aging technology, applied in the field of plastic product manufacturing, can solve the problems of poor anti-aging performance, short life, limited application, etc., and achieve the effect of good dispersion performance, polyester quality and processing performance improvement
- Summary
- Abstract
- Description
- Claims
- Application Information
AI Technical Summary
Problems solved by technology
Method used
Examples
Embodiment 1
[0030] Embodiment 1: A kind of manufacture method of enhanced flame-retardant anti-aging polyester film, adopts following steps:
[0031] A) 2 parts by mass of nanoscale barium acid, 0.5 part of laurylamine, 2 parts of white carbon black, 2 parts of nanoscale organic magnesium hydroxide whiskers, 2 parts of carbonic acid with a diameter of 1 μm and a length of 5 μm. Calcium whisker, 1 part of microencapsulated red phosphorus flame retardant, 0.2 part of silane coupling agent, 4 parts of p-hydroxybenzoic acid, 40 parts of ethylene glycol, 5 parts of 1,3-propanediol, after mixing, stir at 50 ° C Ball mill airtight grinding reaction for 8 hours to obtain flame retardant and enhanced functional alcohol, which can be used up within 48 hours at 70°C;
[0032] B) 2 parts by mass of rutile titanium dioxide, 2 parts of nano-montmorillonite, 4 parts of barium stearate, 0.1 part of silane coupling agent, 0.8 part of triazine-5 light stabilizer, 0.8 part of high temperature antioxidant ,...
Embodiment 2
[0035] Embodiment 2: A kind of manufacture method of enhanced flame-retardant anti-aging polyester film, adopts following steps:
[0036] A) 3 parts by mass of nano-scale barium acid, 1 part of laurylamine, 3 parts of white carbon black, 3 parts of nano-scale organic magnesium hydroxide whiskers, 3 parts of carbonic acid with a diameter of 2 μm and a length of 15 μm Calcium whiskers, 1.5 parts of microencapsulated red phosphorus flame retardant, 0.3 parts of silane coupling agent, 6 parts of p-hydroxybenzoic acid, 45 parts of ethylene glycol, 7.5 parts of 1,3-propanediol, after mixing, stir at 55 ° C Ball mill airtight grinding reaction for 10 hours to obtain flame retardant and enhanced functional alcohol, which can be used up within 48 hours at 70°C;
[0037] B) 3 parts by mass of rutile titanium dioxide, 3 parts of nano-montmorillonite, 6 parts of barium stearate, 0.2 part of silane coupling agent, 1 part of triazine-5 light stabilizer, 1 part of high temperature antioxidan...
Embodiment 3
[0040] Embodiment 3: A kind of manufacturing method of enhanced flame-retardant anti-aging polyester film, adopts following steps:
[0041] A) 4 parts of nanoscale flow acid barium, 1.5 parts of laurylamine, 4 parts of white carbon black, 4 parts of nanoscale organic magnesium hydroxide whiskers, 4 parts of carbonic acid with a diameter of 3 μm and a length of 25 μm in parts by mass Calcium whisker, 2 parts of microencapsulated red phosphorus flame retardant, 0.5 part of silane coupling agent, 8 parts of p-hydroxybenzoic acid, 50 parts of ethylene glycol, 10 parts of 1,3-propanediol, after mixing, stir at 60 ° C Ball mill airtight grinding reaction for 12 hours to obtain flame retardant and enhanced functional alcohol, which can be used up within 48 hours at 70°C;
[0042] B) 4 parts by mass of rutile titanium dioxide, 4 parts of nano-montmorillonite, 8 parts of barium stearate, 0.3 parts of silane coupling agent, 1.2 parts of triazine-5 light stabilizer, 1.2 parts of high-tem...
PUM
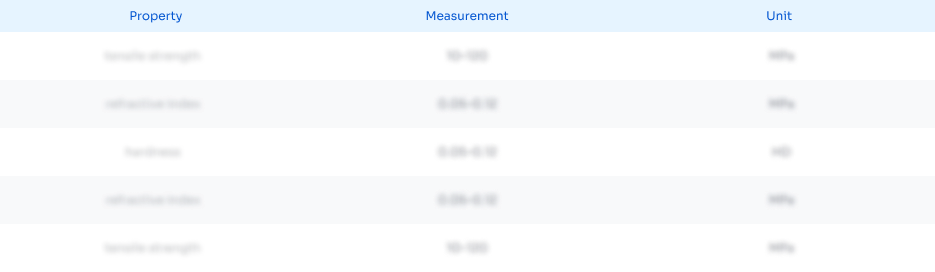
Abstract
Description
Claims
Application Information

- R&D Engineer
- R&D Manager
- IP Professional
- Industry Leading Data Capabilities
- Powerful AI technology
- Patent DNA Extraction
Browse by: Latest US Patents, China's latest patents, Technical Efficacy Thesaurus, Application Domain, Technology Topic, Popular Technical Reports.
© 2024 PatSnap. All rights reserved.Legal|Privacy policy|Modern Slavery Act Transparency Statement|Sitemap|About US| Contact US: help@patsnap.com