High-belite sulphoaluminate cement-based hardener for concrete floor and preparation method of high-belite sulphoaluminate cement-based hardener
A special sulfur aluminate, cement-based technology, applied in the field of concrete, can solve problems such as hollowing delamination, plastic cracking, etc., and achieve the effects of performance enhancement, ultra-high strength and surface hardness, and ultra-high bond strength
- Summary
- Abstract
- Description
- Claims
- Application Information
AI Technical Summary
Problems solved by technology
Method used
Image
Examples
Embodiment 1I
[0023] Embodiment 1I type cement-based hardener
[0024] High Belite Sulphoaluminate Cement: Strength Class 42.5 18%
[0025] Aggregate: 6-10 mesh quartz sand 36%, 40-70 mesh quartz sand 20%, 70-140 mesh quartz sand 5%
[0026] Calcined Kaolin: 5%
[0027] Lime: 1.5%,
[0028] Other mineral admixtures: silica fume 4%, mineral powder 5%
[0029] Rubber powder: 1.0%
[0030] Retarder: tartaric acid 0.05%, citric acid 0.05%
[0031] Water reducer: 0.1%
[0032] Pigment: Titanium Dioxide 2.5%, Iron Oxide Red 1.5%
[0033] The specific performance is shown in Table 1.
[0034] Table 1 Material physical and chemical performance indicators
[0035]
Embodiment 2II
[0036] Embodiment 2Type II cement-based hardener
[0037] High Belite Sulphoaluminate Cement: Strength Class 52.5 16%
[0038] Aggregate: Graded Carborundum 63%
[0039] Calcined Kaolin: 5%
[0040] Lime: 1.5%,
[0041] Other mineral admixtures: silica fume 4%, mineral powder 5%
[0042] Rubber powder: 1.0%
[0043] Retarder: tartaric acid 0.05%, citric acid 0.05%
[0044] Water reducer: 0.1%
[0045] Pigment: Titanium Dioxide 2.0%, Carbon Black 2.5%
[0046] The specific performance is shown in Table 2.
[0047] Table 2 Physical and chemical performance indicators of materials
[0048]
Embodiment 3I
[0049] Embodiment 3I type cement-based hardener
[0050] High Belite Sulphoaluminate Cement: Strength Grade 42.5 19.5%
[0051] Aggregate: 6-10 mesh quartz sand 36%, 40-70 mesh quartz sand 20%, 70-140 mesh quartz sand 5% Calcined kaolin: 5%
[0052] Lime: 1.5%,
[0053] Other mineral admixtures: silica fume 4%, mineral powder 5%
[0054] Rubber powder: 1.0%
[0055] Retarder: tartaric acid 0.05%, citric acid 0.05%
[0056] Water reducer: 0.1%
[0057] Pigment: Titanium Dioxide 2.5%
[0058] The specific performance is shown in Table 3.
[0059] Table 3 Physical and chemical performance indicators of materials
[0060]
[0061]
PUM
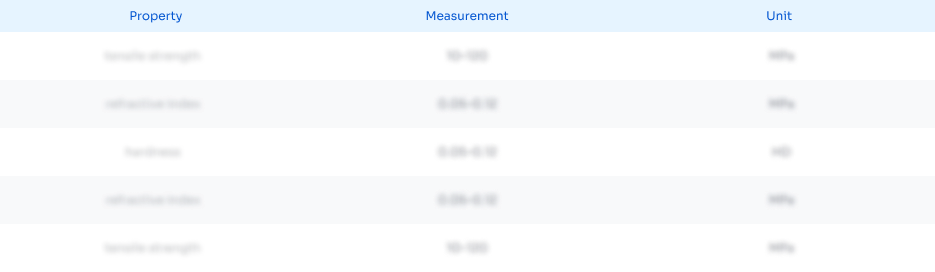
Abstract
Description
Claims
Application Information

- Generate Ideas
- Intellectual Property
- Life Sciences
- Materials
- Tech Scout
- Unparalleled Data Quality
- Higher Quality Content
- 60% Fewer Hallucinations
Browse by: Latest US Patents, China's latest patents, Technical Efficacy Thesaurus, Application Domain, Technology Topic, Popular Technical Reports.
© 2025 PatSnap. All rights reserved.Legal|Privacy policy|Modern Slavery Act Transparency Statement|Sitemap|About US| Contact US: help@patsnap.com