Vacuum induction smelting method for nickel-based superalloy
A technology for vacuum induction melting and nickel-based superalloy, which is applied in the field of vacuum induction melting of nickel-based superalloy, and can solve the problem of inability to remove nitrogen as a gas element, and achieve the effects of reducing nitrogen content, expanding application fields, and increasing surface area.
- Summary
- Abstract
- Description
- Claims
- Application Information
AI Technical Summary
Problems solved by technology
Method used
Examples
Embodiment 1
[0036] Preparation of GH4169 Alloy
[0037] Step 1, alloy melting:
[0038] 1.1 Surface treatment is carried out on the alloy raw material, and it is dried at 100°C for 20 hours.
[0039] 1.2 According to the mass percentage of the target alloy composition raw materials: 20%-Ni, 100% Fe, 100% C, 100% MoFe, 50% Ni, arrange them in the crucible from bottom to top in order, and then place the crucible on The vacuum induction furnace is used for melting, and when the vacuum degree of the furnace chamber is less than 0.1Pa, the electric melting starts. During the melting process, the power is increased slowly and stepwise, with an increasing frequency of 3kW / min, until it reaches the rated melting power, so that the gas elements in the raw materials are gradually released, and the remaining Ni is added during the melting process. The melting rate is less than or equal to 1 / 4 of the maximum furnace capacity / h.
[0040] Step 2, initial refinement:
[0041] After all the materials...
Embodiment 2
[0047] Preparation of GH4698 alloy
[0048] Step 1, alloy melting:
[0049]1.1 Surface treatment is carried out on the alloy raw material, and it is dried at 100°C for 20 hours.
[0050] 1.2 According to the mass percentage of the target alloy composition raw materials: 30% Ni, 100% Fe, 100% C, 100% Mo, 50% Ni, arranged in the crucible from bottom to top in order, and then put the crucible in a vacuum The induction furnace is used for smelting, and when the vacuum degree of the furnace chamber is less than 0.1Pa, the electric smelting starts. During the melting process, the power is increased slowly and stepwise, with an increasing frequency of 3kW / min, until it reaches the rated melting power, so that the gas elements in the raw materials are gradually released, and the remaining Ni is added during the melting process. The melting rate is less than or equal to 1 / 4 of the maximum furnace capacity / h.
[0051] Step 2, initial refinement:
[0052] After all the materials in t...
Embodiment 3
[0058] Preparation of In718 alloy
[0059] Step 1, alloy melting:
[0060] 1.1 Surface treatment is carried out on the alloy raw material, and it is dried at 100°C for 20 hours.
[0061] 1.2 According to the mass percentage of the target alloy composition raw materials: 25% Ni, 100% Fe, 100% C, 100% MoFe, 40% Ni are arranged in the crucible from bottom to top in order, and then the crucible is placed in a vacuum The induction furnace is used for smelting, and when the vacuum degree of the furnace chamber is less than 0.1Pa, the electric smelting starts. During the melting process, the power is increased slowly and stepwise, with an increasing frequency of 3kW / min, until it reaches the rated melting power, so that the gas elements in the raw materials are gradually released, and the remaining Ni is added during the melting process. The melting rate is less than or equal to 1 / 4 of the maximum furnace capacity / h.
[0062] Step 2, initial refinement:
[0063] After all the mat...
PUM
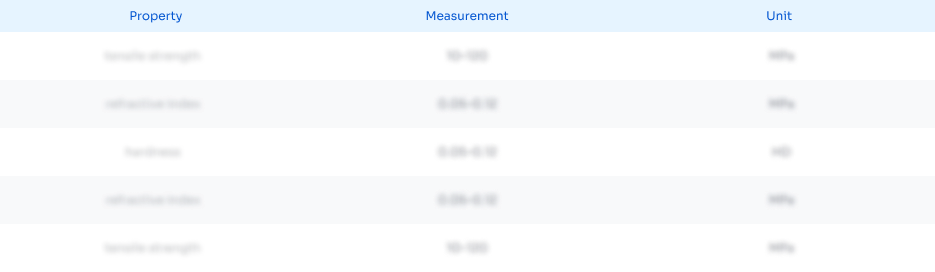
Abstract
Description
Claims
Application Information

- R&D
- Intellectual Property
- Life Sciences
- Materials
- Tech Scout
- Unparalleled Data Quality
- Higher Quality Content
- 60% Fewer Hallucinations
Browse by: Latest US Patents, China's latest patents, Technical Efficacy Thesaurus, Application Domain, Technology Topic, Popular Technical Reports.
© 2025 PatSnap. All rights reserved.Legal|Privacy policy|Modern Slavery Act Transparency Statement|Sitemap|About US| Contact US: help@patsnap.com