Slagging agent for separating silicon slag during polysilicon medium smelting and its application method
A medium smelting and slagging agent technology, applied in chemical instruments and methods, silicon compounds, inorganic chemistry, etc., can solve the problems of difficult separation of silicon slag, large loss of silicic acid, and low recovery rate
- Summary
- Abstract
- Description
- Claims
- Application Information
AI Technical Summary
Problems solved by technology
Method used
Examples
Embodiment 1
[0023] Slagging agent is selected, which is made by mixing the following raw materials: SiO 2 50%, CaO35% and CaCl 2 15%.
[0024] The method of using the slagging agent that facilitates the separation of silicon slag during polysilicon medium smelting is carried out according to the following steps:
[0025] (1) Add 100kg of silicon material into the graphite crucible, use an intermediate frequency induction furnace to increase the power to 150W, and melt all the silicon material into silicon liquid after 60 minutes;
[0026] (2) Add the slagging agent into the mixer according to the raw material composition and mix evenly, and the mixing time is 10 minutes;
[0027] (3) Take 50kg of the mixed slagging agent, divide it into 5 parts, add it in order at intervals of 10 minutes, and keep the power at 100kW. After adding it completely, keep the power at 100kW, keep the temperature of the upper surface of the melt at 1650°C, and keep it warm for 35 minutes for medium melting ; ...
Embodiment 2
[0031] Slagging agent is selected, which is made by mixing the following raw materials: SiO 2 60%, CaO30% and CaCl 2 10%.
[0032] The method of using the slagging agent that facilitates the separation of silicon slag during polysilicon medium smelting is carried out according to the following steps:
[0033] (1) Add 100kg of silicon material into the graphite crucible, use an intermediate frequency induction furnace to increase the power to 100kW, and melt all the silicon material into silicon liquid after 80 minutes;
[0034] (2) Add the slagging agent into the mixer according to the raw material composition and mix evenly, and the mixing time is 15 minutes;
[0035] (3) Take 100kg of the mixed slagging agent, divide it into 10 parts, add it in order at intervals of 15 minutes, and keep the power at 50kW. After adding it completely, keep the power at 50kW, keep the temperature of the upper surface of the melt at 1700°C, and keep it warm for 60 minutes for medium melting ;...
Embodiment 3
[0039] Slagging agent is selected, which is made by mixing the following raw materials: SiO 2 70%, CaO20% and CaCl 2 10%.
[0040] The method of using the slagging agent that facilitates the separation of silicon slag during polysilicon medium smelting is carried out according to the following steps:
[0041] (1) Add 100kg of silicon material into the graphite crucible, use an intermediate frequency induction furnace to increase the power to 200kW, and melt all the silicon material into silicon liquid after 40 minutes;
[0042] (2) Add the slagging agent into the mixer according to the raw material composition and mix evenly, and the mixing time is 20 minutes;
[0043] (3) Take 30kg of the mixed slagging agent, divide it into 6 equal portions, add them in order at intervals of 10 minutes, and keep the power at 200kW. After adding it completely, keep the power at 150kW, keep the temperature of the upper surface of the melt at 1750°C, and keep it warm for 20 minutes for medium...
PUM
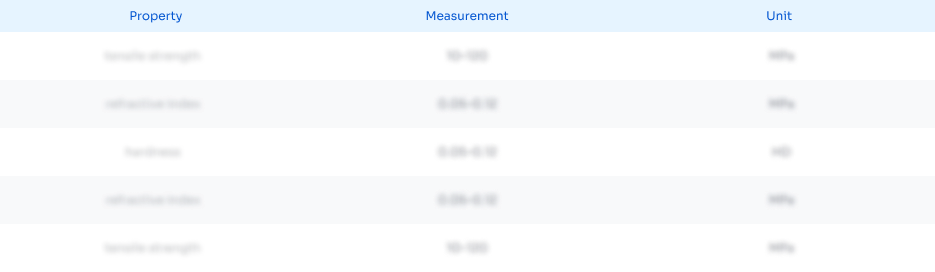
Abstract
Description
Claims
Application Information

- R&D
- Intellectual Property
- Life Sciences
- Materials
- Tech Scout
- Unparalleled Data Quality
- Higher Quality Content
- 60% Fewer Hallucinations
Browse by: Latest US Patents, China's latest patents, Technical Efficacy Thesaurus, Application Domain, Technology Topic, Popular Technical Reports.
© 2025 PatSnap. All rights reserved.Legal|Privacy policy|Modern Slavery Act Transparency Statement|Sitemap|About US| Contact US: help@patsnap.com