Process performing methanation on gas synthesized by coal to synthesize substitute natural gas
A technology for replacing natural gas and coal to syngas, which is applied in the petroleum industry, gas fuel, fuel and other directions to achieve the effects of reducing reaction energy consumption, reducing reactor load, and avoiding sintering deactivation
- Summary
- Abstract
- Description
- Claims
- Application Information
AI Technical Summary
Problems solved by technology
Method used
Image
Examples
Embodiment 1
[0039] The catalysts for reactors R1 and R2 are first prepared. The preparation process is as follows: prepare a nickel nitrate solution with a cation concentration of 0.5 g / ml, and add 10-40 mesh γ-Al 2 o 3 The carrier powder is impregnated for 12 hours under stirring conditions. After the impregnation, the suspension is heated and concentrated in a water bath at 60°C, then calcined at 550°C for 6 hours, and ground to 10-40 mesh after calcining. The catalyst preparation steps used in reactors R2, R3, R4, and R5 are the same as above, and the specific parameters are shown in Attached Table 1 and Attached Table 2.
[0040] The catalyst and quartz sand are mixed and loaded. The mass ratio of catalyst to quartz sand in reactors R1 and R2 is 1:0.8, and the ratio of catalyst to quartz sand in reactor R3 is 1:0.5. Reactors R4 and R5 are filled with catalyst only.
[0041] The metal active components in the loaded catalyst are in an oxidized state and need to be pre-reduced after...
Embodiment 2-11
[0045] On the basis of Example 1, the ratio of height to diameter of the reactor catalyst bed, space velocity, reaction pressure, hydrogen-to-carbon ratio of synthesis gas, distribution ratio of synthesis gas, reactor inlet temperature, synthesis gas and water vapor in Examples 2-11 The molar ratio, reactor outlet temperature, catalyst active component type, active component content, catalyst and quartz sand mass ratio factors have been adjusted. The specific data and results are shown in Attached Table 1, and the catalyst preparation conditions used in the reaction are shown in Attached Table 2 , see attached table 3 for composition of feed gas and product gas, see attached table 4 for reduction conditions. All the other are with embodiment 1.
[0046]
[0047]
[0048]
[0049] Schedule 3
[0050]
[0051] Schedule 4
[0052]
PUM
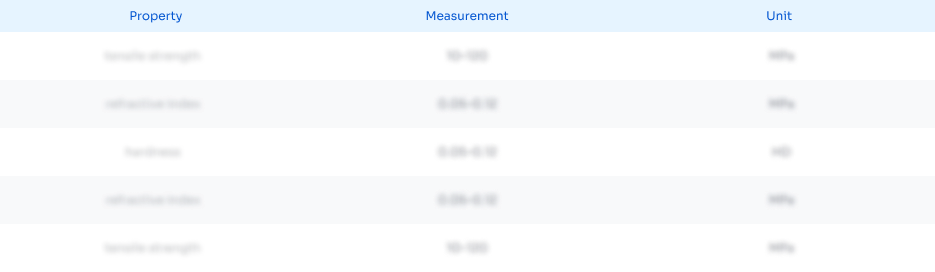
Abstract
Description
Claims
Application Information

- Generate Ideas
- Intellectual Property
- Life Sciences
- Materials
- Tech Scout
- Unparalleled Data Quality
- Higher Quality Content
- 60% Fewer Hallucinations
Browse by: Latest US Patents, China's latest patents, Technical Efficacy Thesaurus, Application Domain, Technology Topic, Popular Technical Reports.
© 2025 PatSnap. All rights reserved.Legal|Privacy policy|Modern Slavery Act Transparency Statement|Sitemap|About US| Contact US: help@patsnap.com