Coating film, method for forming coating film, and light-emitting diode device
A light-emitting diode and coating film technology, which is applied in the direction of electric solid-state devices, semiconductor devices, electric light sources, etc., can solve the problems of uneven activation of materials formed by spray coating, poor appearance of dirt, and difficulties in coating films, etc., and achieve wire bonding Excellent properties, excellent oxidation resistance, and excellent safety effects
- Summary
- Abstract
- Description
- Claims
- Application Information
AI Technical Summary
Problems solved by technology
Method used
Image
Examples
Embodiment 1~21、 comparative example 1~7
[0089] In Examples 1 to 21 and Comparative Examples 1 to 7, samples obtained by performing silver plating (brightness L value: 70) with a thickness of 4 μm on a pure copper substrate by an electrolytic plating method were used. The base material is formed into a coating film treated with the atmospheric pressure plasma polymerization of the present invention. The conditions of the atmospheric pressure plasma polymerization treatment at this time are as follows.
[0090] (Conditions for Atmospheric Pressure Plasma Polymerization Treatment)
[0091] The transmission frequency of the plasma generator: 21kHz
[0092] Generator output voltage: 280V
[0093] Pressure: atmospheric pressure (1013.25hPa)
[0094] Import amount of hexamethyldisiloxane: 20g / h
[0095] Carrier gas and plasma gas: nitrogen (nitrogen content: 100%)
[0096] In addition, in Examples 1 to 21 and Comparative Examples 1 to 7, the nozzle distance and the nozzle moving speed at the time of forming the coatin...
Embodiment 22、23
[0113] In Example 22, a sample obtained in the same manner as in Example 1 was used except that decamethyltetrasiloxane (DMTSO) was used as the material of the coating film. In addition, in Example 23, a sample obtained in the same manner as in Example 1 was used except that octamethylcyclotetrasiloxane (OMCTSO) was used as the material of the coating film.
[0114] The coating films formed on the surfaces of these samples were analyzed using an infrared spectroscopic analyzer. As a result, it was confirmed that these coating films were all composed of the structural formula: (CH 3 ) 3 SiO-[(CH 3 ) 2 SiO] n -Si(CH 3 ) 3 Indicates the composition of dimethylpolysiloxane. Moreover, as a result of evaluating the above-mentioned (a)-(c) about this sample, it was confirmed that it has the characteristic equivalent to Examples 1-21.
Embodiment 24
[0116] A sample obtained in the same manner as in Example 1 was used except that a material in which a part of the side chain of hexamethyldisiloxane (HMDSO) was substituted with a carboxyl group was used as the material of the coating film.
[0117] The coating film formed on the surface of the sample was analyzed using an infrared lead spectrometer, and as a result, it was confirmed that the coating film was composed of the structural formula: (CH 3 ) 3 SiO-[(CH 3 ) 2 SiO] m -[(C 6 h 5 ) 2 SiO] n -Si(CH 3 ) 3 Represents the composition of methylphenyl polysiloxane. Moreover, as a result of evaluating the above-mentioned (a)-(c) about this sample, it was confirmed that it has the characteristic equivalent to Examples 1-21.
PUM
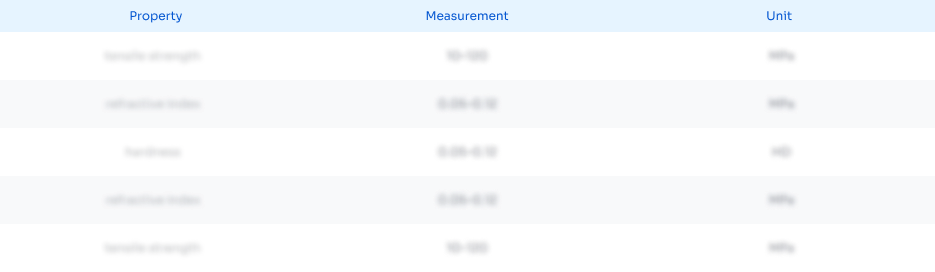
Abstract
Description
Claims
Application Information

- Generate Ideas
- Intellectual Property
- Life Sciences
- Materials
- Tech Scout
- Unparalleled Data Quality
- Higher Quality Content
- 60% Fewer Hallucinations
Browse by: Latest US Patents, China's latest patents, Technical Efficacy Thesaurus, Application Domain, Technology Topic, Popular Technical Reports.
© 2025 PatSnap. All rights reserved.Legal|Privacy policy|Modern Slavery Act Transparency Statement|Sitemap|About US| Contact US: help@patsnap.com