Method for preparing lithium carbonate from lepidolite
A technology of lithium carbonate and lepidolite, which is applied in the direction of lithium carbonate;/acid carbonate, etc., can solve the problems of low leaching rate of valuable metals, low utilization rate of raw materials, and restrictions on large-scale production, and achieve effective Conducive to large-scale production, energy saving, and the effect of improving recovery rate
- Summary
- Abstract
- Description
- Claims
- Application Information
AI Technical Summary
Problems solved by technology
Method used
Image
Examples
Embodiment 1
[0030] First mix lepidolite (100-500 mesh) and 98% concentrated sulfuric acid at a ratio of 1:1 with a mixer, and then dry it twice in a drying kiln (100-350°C and 200-500°C each 2-4 hours), during the drying process, the sulfuric acid and the metal ions in lepidolite fully react, not only replacing all the metal ions, but also consuming all the sulfuric acid, which improves the lithium leaching rate and reduces the pressure of subsequent neutralization. The dried material is clinker, and the dried clinker is crushed again into 100-500 mesh by a crusher, and then soaked and stirred in an enamel reaction tank with twice the amount of water and boiled for 30-60 minutes, lithium and other metal ions All dissolved in water into liquid phase. In the actual reaction, drying can be carried out more than two times according to the need, and the drying conditions are consistent with the above.
[0031] After water leaching, the mixed solution is separated from the solid and liquid thr...
Embodiment 2
[0036] First mix lepidolite (100-500 mesh) and 98% concentrated sulfuric acid at a ratio of 1:0.8 with a mixer, and then dry twice in a drying kiln (100-350°C and 200-500°C each 2-4 hours), during the drying process, the sulfuric acid and the metal ions in lepidolite fully react, not only replacing all the metal ions, but also consuming all the sulfuric acid, which improves the lithium leaching rate and reduces the pressure of subsequent neutralization. The dried material is clinker, and the dried clinker is crushed again into 100-500 mesh by a crusher, and then soaked and stirred in an enamel reaction tank with twice the amount of water and boiled for 30-60 minutes, lithium and other metal ions All dissolved in water into liquid phase. In the actual reaction, drying can be carried out more than two times according to the need, and the drying conditions are consistent with the above.
[0037] After water leaching, the mixed solution is separated from the solid and liquid thro...
Embodiment 3
[0043] First mix lepidolite (100-500 mesh) and 98% concentrated sulfuric acid at a ratio of 1:2 with a mixer, and then dry twice in a drying kiln (100-350°C and 200-500°C each 2-4 hours), during the drying process, all the metal ions are replaced, which improves the lithium leaching rate and reduces the pressure of subsequent neutralization. The dried material is clinker, and the dried clinker is crushed again into 100-500 mesh by a crusher, and then soaked and stirred in an enamel reaction tank with twice the amount of water and boiled for 30-60 minutes, lithium and other metal ions All dissolved in water into liquid phase. In the actual reaction, drying can be carried out more than two times according to the need, and the drying conditions are consistent with the above.
[0044] After water leaching, the mixed solution is separated from the solid and liquid through the centrifuge while it is still hot (≥90°C), and the solid residue is washed and dried by the centrifuge, and...
PUM
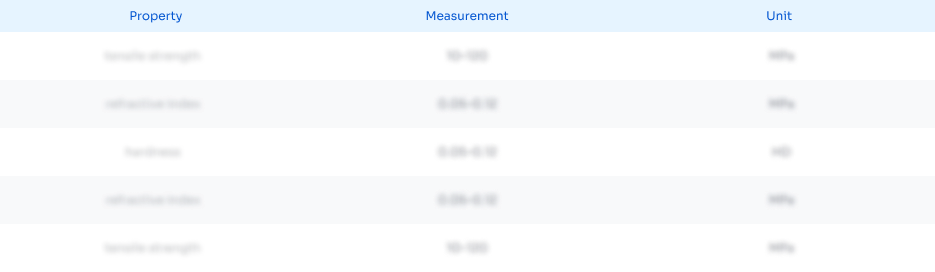
Abstract
Description
Claims
Application Information

- R&D
- Intellectual Property
- Life Sciences
- Materials
- Tech Scout
- Unparalleled Data Quality
- Higher Quality Content
- 60% Fewer Hallucinations
Browse by: Latest US Patents, China's latest patents, Technical Efficacy Thesaurus, Application Domain, Technology Topic, Popular Technical Reports.
© 2025 PatSnap. All rights reserved.Legal|Privacy policy|Modern Slavery Act Transparency Statement|Sitemap|About US| Contact US: help@patsnap.com