Manufacturing method of metal-based circuit board of LED
A technology for metal-based circuit boards and manufacturing methods, which is applied in the fields of printed circuit manufacturing, circuit substrate materials, and printed circuit precursor manufacturing, can solve the problems of slow production speed, waste of raw materials, and increased production costs, and achieve strong thermal conductivity. Strong adhesion and high pressure resistance
- Summary
- Abstract
- Description
- Claims
- Application Information
AI Technical Summary
Problems solved by technology
Method used
Image
Examples
Embodiment 1
[0029] refer to figure 1 , figure 2 As shown, a method for manufacturing an LED metal-based circuit board usually includes two parts: making a metal-based copper-clad laminate and making a metal-based circuit board based on it. The steps include:
[0030] Manufacture of metal-based copper clad laminates
[0031] (1) Surface treatment of the metal plate: select an aluminum plate with a thickness of 0.2 mm, degrease, roughen, clean, and dry the surface to obtain an aluminum base plate.
[0032] (2) Overlapping thermally conductive insulating film: it is to laminate the thermally conductive insulating film on the aluminum substrate, among which there are three types of insulating adhesive, among which there are three types of insulating adhesive, ① thermally conductive PP composed of glass cloth and thermally conductive adhesive, ② with Ordinary PP composed of glass cloth and epoxy resin, ③ thermally conductive adhesive film composed of thermally conductive adhesive. And the ...
Embodiment 2
[0046] First, a 1.5mm aluminum plate is selected. The step (5) is different from that of Example 1. This example adopts a printing process to realize circuit diagram formation. The UV curing energy on the surface is 650mj to form a pattern on the substrate surface, and then the copper foil surface is printed and UV cured to form a circuit pattern on the surface of the board. Other steps are the same as in Example 1.
[0047] In the present invention, a copper plate with a thickness of 0.1 mm or 0.2 mm can be selected, and the other steps are the same as in Embodiment 2 to manufacture an integrated LED circuit board integrating a driving electric light source.
Embodiment 3
[0049] First, a 1mm aluminum plate is selected, and step (5) is different from Example 1. In this example, a printing process is used to realize circuit diagram formation. The printing process is printed with UV ink. The UV curing energy of the substrate is 800mj to form a pattern on the substrate surface, and then the copper foil surface is printed and UV cured to form a circuit pattern on the substrate surface. The other steps are the same as in Example 1.
[0050] In the present invention, metal substrates such as iron plates or silicon steel plates can also be selected as substrate materials. In step (5), the exposure process is used to realize the formation of circuit diagrams, and other steps are the same as in embodiment 3.
PUM
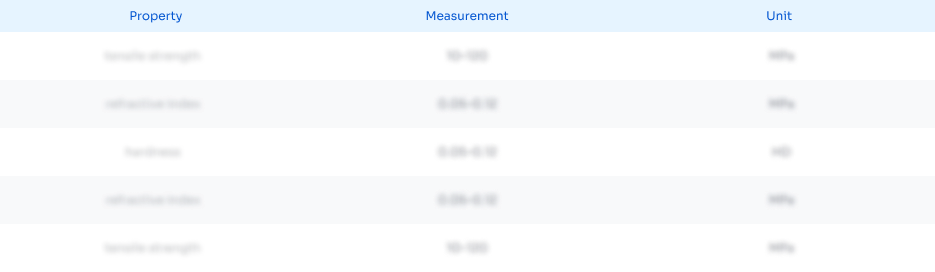
Abstract
Description
Claims
Application Information

- R&D
- Intellectual Property
- Life Sciences
- Materials
- Tech Scout
- Unparalleled Data Quality
- Higher Quality Content
- 60% Fewer Hallucinations
Browse by: Latest US Patents, China's latest patents, Technical Efficacy Thesaurus, Application Domain, Technology Topic, Popular Technical Reports.
© 2025 PatSnap. All rights reserved.Legal|Privacy policy|Modern Slavery Act Transparency Statement|Sitemap|About US| Contact US: help@patsnap.com