Process for producing 1,4-butanediol
A technology of butanediol and butanol, applied in chemical instruments and methods, preparation of organic compounds, organic chemistry, etc., can solve the problems of poor economy and high energy consumption, and achieve the effect of saving energy consumption and waste water generation
- Summary
- Abstract
- Description
- Claims
- Application Information
AI Technical Summary
Problems solved by technology
Method used
Image
Examples
Embodiment 1
[0034] according to figure 1 In the process shown, the mixture flow 1 using n-butane, air and water vapor as raw materials enters the reaction unit R, and reacts to obtain the flow 2 containing maleic anhydride, water, nitrogen, acetic acid, acrylic acid and butane. Stream 2 is heat-exchanged to about 130°C by switching coolers. Enter the absorption tower A, and obtain an oil-rich stream 4 containing 12%-18% maleic anhydride through absorption and separation. Stream 4 enters the esterification unit E, reacts with butanol in the stream 8 and stream 14 entering the esterification unit, obtains dibutyl maleate from the bottom of the esterification tower, and the maleic acid at the bottom of the esterification tower The dibutyl ester stream 5 enters the absorption tower A; the esterification tower overhead stream 7 enters the light tower, and after rectification, the light component stream 71 and stream 75 are mixed into the chromatograph, and the heavy stream 77 enters the heavy...
Embodiment 2
[0054] According to the conditions and steps described in Example 1, the weight content of n-butane in feed stream 1 was 3.5%, the weight content of oxygen was 22.0%, and the temperature was 150°C. The operating conditions of n-butane oxidation reactor R are: operating temperature 400°C, operating pressure 2.18 bar.
[0055] The operating conditions of absorption tower A are as follows: the number of trays is 25, the operating temperature at the top of the tower is 80.0°C, the temperature at the bottom of the tower is 90.0°C, the pressure at the top of the tower is 1.4bar, the temperature of the cold cycle in the middle and lower section of the tower is 40.0°C, and the number of circulating feeding plates is 18 pieces, the ratio of the weight of the circulating stream to the weight of the stream 4 is 4.56.
[0056] The operating conditions of the monoesterification reactor are as follows: the operating temperature is 120° C., and the operating pressure is 9.0 bar. Double este...
Embodiment 3
[0072] According to the conditions and steps described in Example 1, the weight content of n-butane in feed stream 1 was 3.5%, the weight content of oxygen was 22.0%, and the temperature was 150°C. The operating conditions of n-butane oxidation reactor R are: operating temperature 400°C, operating pressure 2.18 bar.
[0073] The operating conditions of absorption tower A are as follows: the number of trays is 25, the operating temperature at the top of the tower is 85.0°C, the temperature at the bottom of the tower is 97.4°C, the pressure at the top of the tower is 1.7bar, the temperature of the cold cycle in the middle and lower section of the tower is 52.0°C, and the number of circulating feeding plates is 18 pieces, the ratio of the weight of the circulating stream to the weight of the stream 4 is 4.56.
[0074] The operating conditions of the monoesterification reactor are as follows: the operating temperature is 120° C., and the operating pressure is 9.0 bar. Double este...
PUM
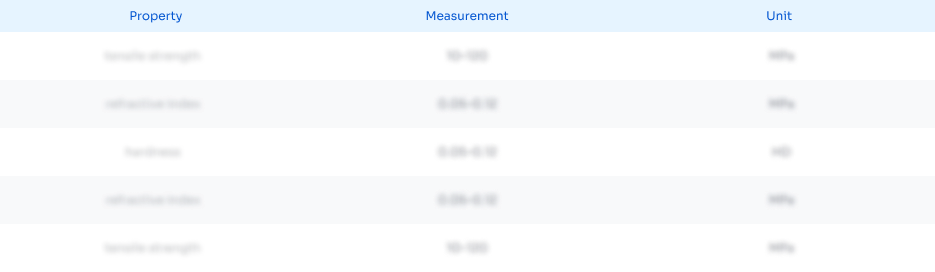
Abstract
Description
Claims
Application Information

- R&D
- Intellectual Property
- Life Sciences
- Materials
- Tech Scout
- Unparalleled Data Quality
- Higher Quality Content
- 60% Fewer Hallucinations
Browse by: Latest US Patents, China's latest patents, Technical Efficacy Thesaurus, Application Domain, Technology Topic, Popular Technical Reports.
© 2025 PatSnap. All rights reserved.Legal|Privacy policy|Modern Slavery Act Transparency Statement|Sitemap|About US| Contact US: help@patsnap.com