Manufacturing method of back surface polishing crystalline silicon solar battery
A technology for solar cells and manufacturing methods, applied in the direction of final product manufacturing, sustainable manufacturing/processing, circuits, etc., can solve the problems of corrosion of the N-type diffusion layer of the solar cell, damage to the PN junction of the solar cell, and reduction of the conversion efficiency of the solar cell. , to achieve the effect of improving uniformity, avoiding damage, and improving photoelectric conversion efficiency
- Summary
- Abstract
- Description
- Claims
- Application Information
AI Technical Summary
Problems solved by technology
Method used
Image
Examples
Embodiment Construction
[0019] The specific embodiments of the present invention are described by taking the manufacturing of a back surface polished local point contact crystalline silicon solar cell as an example.
[0020] The manufacturing process of the back surface polishing local point contact crystalline silicon solar cell is as follows Figure 4 As shown, it includes: back surface coating, texturing and cleaning before diffusion, diffusion, wet etching and PSG removal, silicon nitride film coating on the front surface, aluminum oxide film coating on the back surface, laser Grooving, screen printing and sintering. The following is a detailed description of each process, the specific content is as follows:
[0021] 1. Coating on the back surface
[0022] Use as Figure 5 (A) The ordinary P-type silicon wafer as shown. The main purpose of the back surface coating process is to plate a layer of mask 8 on the back surface of the P-type silicon wafer as a protective layer on the back surface, such as ...
PUM
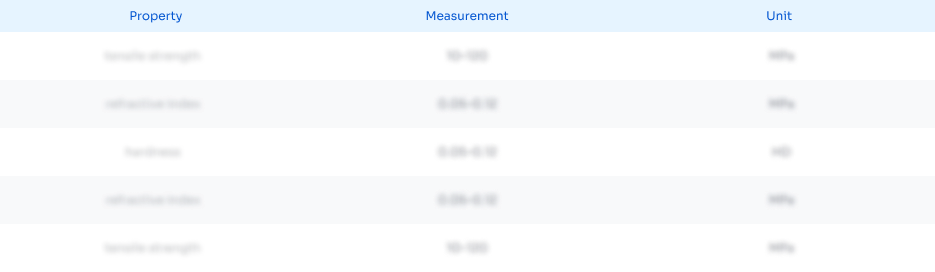
Abstract
Description
Claims
Application Information

- R&D
- Intellectual Property
- Life Sciences
- Materials
- Tech Scout
- Unparalleled Data Quality
- Higher Quality Content
- 60% Fewer Hallucinations
Browse by: Latest US Patents, China's latest patents, Technical Efficacy Thesaurus, Application Domain, Technology Topic, Popular Technical Reports.
© 2025 PatSnap. All rights reserved.Legal|Privacy policy|Modern Slavery Act Transparency Statement|Sitemap|About US| Contact US: help@patsnap.com