Gradual type laser shock continuous riveting method and device
A laser shock and progressive technology, applied in the direction of laser welding equipment, welding equipment, metal processing equipment, etc., can solve the problem of damage to material integrity and sealing, small size of mechanical interlocking structure parts, difficulty in controlling the direction of lateral force, etc. Problems, avoid electrochemical corrosion, improve surface quality, and have a large degree of deformation
- Summary
- Abstract
- Description
- Claims
- Application Information
AI Technical Summary
Problems solved by technology
Method used
Image
Examples
Embodiment
[0053]Embodiment: a kind of progressive laser shock continuous riveting device, its structure is as follows figure 1 As shown, it includes a control module 1, a pulse laser 2 connected to the control module and an articulated robot 3, a water storage tank 7 on one side of the joint robot 3, a water curtain generator 5 installed on the water storage tank 7, and The water pump 6 used to pump the water in the water storage tank 7 to the water curtain generator 5.
[0054] A forming mold 8 is installed on the water storage tank 7, and the forming mold includes a base 8a; two L-shaped support frames 8b inverted on the base, and the non-closed space formed by the two L-shaped support frames and the base is formed by plates. The forming cavity of the lock structure.
[0055] The pulsed laser 2 can output pulsed lasers with adjustable parameters, which are divided into at least two beams by the optical splitting system 10, and transmitted to the first laser focusing lens 9a and the s...
PUM
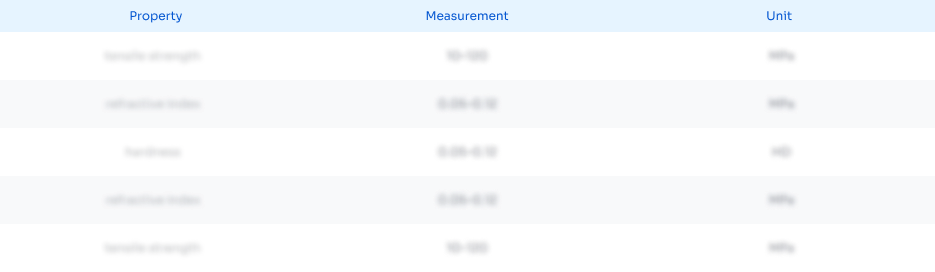
Abstract
Description
Claims
Application Information

- Generate Ideas
- Intellectual Property
- Life Sciences
- Materials
- Tech Scout
- Unparalleled Data Quality
- Higher Quality Content
- 60% Fewer Hallucinations
Browse by: Latest US Patents, China's latest patents, Technical Efficacy Thesaurus, Application Domain, Technology Topic, Popular Technical Reports.
© 2025 PatSnap. All rights reserved.Legal|Privacy policy|Modern Slavery Act Transparency Statement|Sitemap|About US| Contact US: help@patsnap.com