Rolling-extruding composite near-net forming method for large ring piece having outer contour with abrupt-change section
A near-net-shaped, outer contour technology, applied in metal rolling, special data processing applications, geometric CAD, etc., can solve the problems of destroying the integrity of the metal streamline, weakening the mechanical properties of the ring, and low processing efficiency, and achieves a high efficiency. Conducive to forming and filling, small forming force and improved material utilization
- Summary
- Abstract
- Description
- Claims
- Application Information
AI Technical Summary
Problems solved by technology
Method used
Image
Examples
Embodiment Construction
[0063] The present invention will be further described below in conjunction with drawings and embodiments.
[0064] A rolling-extrusion composite near-net-shaping method for rings with abrupt cross-sections of large outer contours, comprising the steps of:
[0065] S1. Pre-roll forming the blank after upsetting and punching to obtain a ring blank with uniform wall thickness and large-diameter rectangular cross-section; figure 2 and image 3 As shown, during pre-roll forming, under the joint action of the driving roll and the core roll, the wall thickness of the billet is reduced, the inner and outer diameters are enlarged, and the height is basically kept unchanged. When the inner and outer diameters reach the designed size, the radial roll forming Finish.
[0066] According to the principle of constant diameter expansion ratio and volume, the size of ring blank 4 after pre-rolling is calculated by the following formula,
[0067]
[0068] Wherein, D, d, B are respective...
PUM
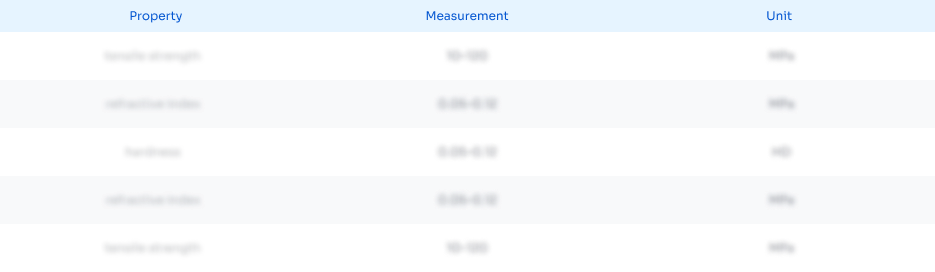
Abstract
Description
Claims
Application Information

- Generate Ideas
- Intellectual Property
- Life Sciences
- Materials
- Tech Scout
- Unparalleled Data Quality
- Higher Quality Content
- 60% Fewer Hallucinations
Browse by: Latest US Patents, China's latest patents, Technical Efficacy Thesaurus, Application Domain, Technology Topic, Popular Technical Reports.
© 2025 PatSnap. All rights reserved.Legal|Privacy policy|Modern Slavery Act Transparency Statement|Sitemap|About US| Contact US: help@patsnap.com