Spherical titanium niobate electrode material and preparation method thereof
An electrode material, titanium niobate technology, applied in battery electrodes, circuits, electrical components, etc., can solve problems such as low battery energy density, and achieve uniform size, easy industrial production, and high reversible capacity.
- Summary
- Abstract
- Description
- Claims
- Application Information
AI Technical Summary
Problems solved by technology
Method used
Image
Examples
Embodiment 1
[0028] 1) Dissolve niobium ethoxide and butyl titanate in a certain amount of isopropanol respectively, and then mix to obtain a mixed solution, wherein the concentration of niobium in the mixed solution is 0.8mol / L, niobium atom:titanium atom=1.8:1 , niobium ethoxide is a kind of niobium source, and butyl titanate is a kind of titanium source;
[0029] 2) Put the solution obtained in step 1) into a reaction kettle, heat the reaction at 158° C. in a constant temperature drying oven, and then naturally cool to room temperature to obtain a precipitate;
[0030] 3) The obtained precipitate was washed several times with deionized water and ethanol, and then vacuum-dried at 50°C to obtain a powder;
[0031] 4) Calcining the powder obtained in step 3) at 1200° C. in a tube furnace to obtain a spherical titanium niobate electrode material.
[0032] The XRD figure of the spherical titanium niobate electrode material prepared by embodiment 1 is as follows figure 1 As shown, the diffr...
Embodiment 2
[0035] 1) Niobium ethoxide and titanium tetrachloride are respectively dissolved in a certain amount of ethylene glycol, and then mixed to obtain a mixed solution, wherein the concentration of niobium in the mixed solution is 3.1mol / L, niobium atom:titanium atom=2.3:1 , niobium ethoxide is a kind of niobium source, and titanium tetrachloride is a kind of titanium source;
[0036] 2) Put the solution obtained in step 1) into a reaction kettle, heat the reaction at 240° C. in a constant temperature drying oven, and then naturally cool to room temperature to obtain a precipitate;
[0037] 3) Naturally cool to room temperature, wash the obtained precipitate several times with deionized water and ethanol, and then vacuum dry at 79°C in a vacuum drying machine to obtain a powder;
[0038] 4) Calcining the powder obtained in step 3) at 760° C. in a tube furnace to obtain a spherical titanium niobate electrode material.
Embodiment 3
[0040] 1) Niobium pentachloride and titanium tetrachloride are respectively dissolved in a certain amount of acetic acid, and then mixed to obtain a mixed solution, wherein the concentration of niobium in the mixed solution is 0.02mol / L, niobium atom:titanium atom=2.15:1 , niobium pentachloride is a kind of niobium source, and titanium tetrachloride is a kind of titanium source;
[0041] 2) Put the solution obtained in step 1) into a reaction kettle, heat the reaction at 70° C. in a constant temperature drying oven, and then naturally cool to room temperature to obtain a precipitate;
[0042] 3) Naturally cool to room temperature, wash the obtained precipitate with deionized water and ethanol several times, and then vacuum dry at 98°C in a vacuum drying machine to obtain a powder;
[0043] 4) Calcining the powder obtained in step 3) at 920° C. in a tube furnace to obtain a spherical titanium niobate electrode material.
PUM
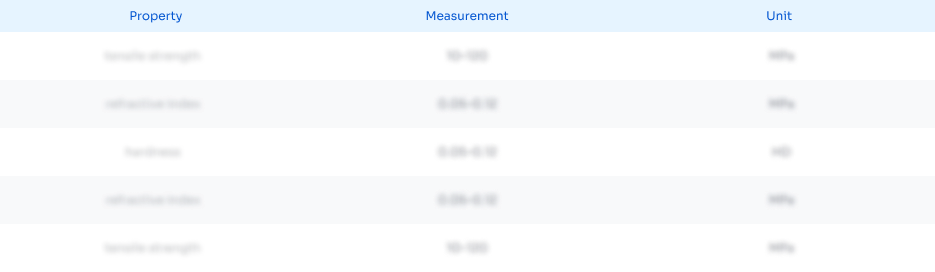
Abstract
Description
Claims
Application Information

- R&D Engineer
- R&D Manager
- IP Professional
- Industry Leading Data Capabilities
- Powerful AI technology
- Patent DNA Extraction
Browse by: Latest US Patents, China's latest patents, Technical Efficacy Thesaurus, Application Domain, Technology Topic, Popular Technical Reports.
© 2024 PatSnap. All rights reserved.Legal|Privacy policy|Modern Slavery Act Transparency Statement|Sitemap|About US| Contact US: help@patsnap.com