A kind of urea-formaldehyde resin paraffin microcapsule material with high thermal conductivity and high enthalpy value and its preparation method
A paraffin microcapsule, high thermal conductivity technology, applied in the direction of heat exchange materials, chemical instruments and methods, can solve the problems of increased production cost, thermal performance impact, reduced microcapsule phase change enthalpy, etc., to achieve uniform coating , the effect of improving thermal conductivity
- Summary
- Abstract
- Description
- Claims
- Application Information
AI Technical Summary
Problems solved by technology
Method used
Examples
Embodiment 1
[0016] Add 5.00g of urea, 0.50g of ammonium chloride, 0.50g of resorcinol and 45.00g of paraffin into 200.00mL of deionized water, raise the temperature to 60°C, keep stirring for 10 minutes (200rpm), then add 12.67g of formaldehyde solution, stirring speed Increase to 10000rpm for 4 hours. The obtained microcapsules are filtered, washed and dried to obtain a powder with uniform particle size distribution. Add 0.50g of graphene oxide (mass ratio of graphene oxide to microcapsules: 1:20), 0.10g of cetyltrimethylammonium bromide (mass ratio of 5:1) and 50mL of deionized water, ultrasonic 30 minutes to obtain a graphene oxide dispersion. Add 10.00 g of the prepared microcapsule powder and 0.10 g of sodium dodecylbenzenesulfonate (mass ratio: 100:1) into 100 mL of deionized water, ultrasonicate for 10 minutes, then add the prepared graphene oxide dispersion, and keep stirring 30 minutes (100rpm), then filtered, washed and dried to obtain graphene oxide-coated urea-formaldehyde r...
Embodiment 2
[0018] Add 5.00g of urea, 0.50g of ammonium chloride, 0.50g of resorcinol and 45.00g of paraffin into 200.00mL of deionized water, raise the temperature to 60°C, keep stirring for 10 minutes (200rpm), then add 12.67g of formaldehyde solution, stirring speed Increase to 10000rpm for 4 hours. The obtained microcapsules are filtered, washed and dried to obtain a powder with uniform particle size distribution. Add 1.00g of graphene oxide (mass ratio of graphene oxide to microcapsules: 1:10), 0.10g of cetyltrimethylammonium bromide (mass ratio of 10:1) into 50mL of deionized water, ultrasonic for 30 minutes , to obtain a graphene oxide dispersion. Add 10.00 g of the prepared microcapsule powder and 0.10 g of sodium dodecylbenzenesulfonate (mass ratio: 100:1) into 100 mL of deionized water, ultrasonicate for 10 minutes, then add the prepared graphene oxide dispersion, and keep stirring 30 minutes (100rpm), then filtered, washed and dried to obtain graphene oxide-coated urea-formal...
PUM
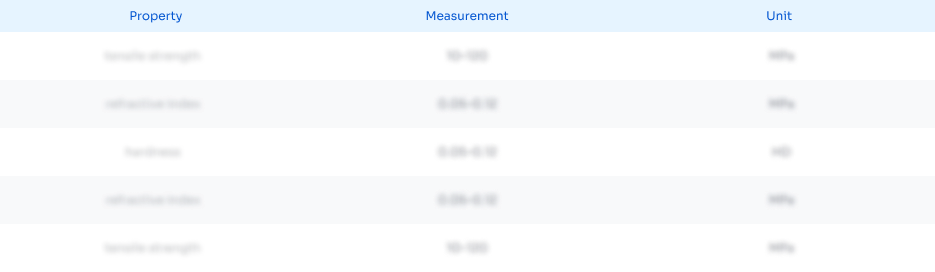
Abstract
Description
Claims
Application Information

- R&D Engineer
- R&D Manager
- IP Professional
- Industry Leading Data Capabilities
- Powerful AI technology
- Patent DNA Extraction
Browse by: Latest US Patents, China's latest patents, Technical Efficacy Thesaurus, Application Domain, Technology Topic, Popular Technical Reports.
© 2024 PatSnap. All rights reserved.Legal|Privacy policy|Modern Slavery Act Transparency Statement|Sitemap|About US| Contact US: help@patsnap.com