Anticorrosive paint for electric system and preparing method thereof
A technology for anti-corrosion coatings and power systems, applied in the field of coatings, can solve the problems of poor high temperature resistance and short anti-corrosion life, and achieve the effects of long service life, low production cost, good alkali resistance and high temperature resistance.
- Summary
- Abstract
- Description
- Claims
- Application Information
AI Technical Summary
Problems solved by technology
Method used
Image
Examples
Embodiment 1
[0016] An anti-corrosion coating for power systems, which is composed of the following raw materials in parts by weight: 23 parts of organic fluorosilicone resin, 18 parts of vulcanized rubber, 13 parts of carbon nanotubes, 26 parts of composite conductive filler, 1 part of ammonium polyphosphate, and 6 parts of propanol , 3 parts of butyl glycidyl ether, 2 parts of zinc stearate, 2 parts of silane coupling agent and 1 part of bentonite.
[0017] Step 1: Add carbon nanotubes to mixed acid and stir with a magnetic stirrer, then condense and reflux, react at 60°C for 2h, then wash with deionized water until neutral, then suction filter, and vacuum dry at 80°C for 24h to obtain Modified carbon nanotubes;
[0018] Step 2, put the composite conductive filler, butyl glycidyl ether, zinc stearate and ammonium polyphosphate into a ball mill, grind for 15 minutes at a speed of 1200 rpm, and then filter the mixture with a 150-mesh sieve;
[0019] Step 3, put organic fluorosilicone resi...
Embodiment 2
[0022] An anti-corrosion coating for power systems, which is composed of the following raw materials in parts by weight: 28 parts of organic fluorosilicone resin, 23 parts of vulcanized rubber, 18 parts of carbon nanotubes, 32 parts of composite conductive filler, 3 parts of ammonium polyphosphate, and 11 parts of propanol , 5 parts of butyl glycidyl ether, 4 parts of zinc stearate, 4 parts of silane coupling agent and 2 parts of bentonite.
[0023] Step 1: Add carbon nanotubes to mixed acid and stir with a magnetic stirrer, then condense and reflux, react at 75°C for 3h, then wash with deionized water until neutral, then vacuum-dry at 90°C for 24h to obtain Modified carbon nanotubes;
[0024] Step 2, put the composite conductive filler, butyl glycidyl ether, zinc stearate and ammonium polyphosphate into a ball mill, grind at a speed of 1500 rpm for 20 minutes, and then filter the mixture with a 200-mesh sieve;
[0025] Step 3, put organic fluorosilicone resin, vulcanized rub...
Embodiment 3
[0028] An anti-corrosion coating for power systems, which is composed of the following raw materials in parts by weight: 32 parts of organic fluorosilicone resin, 28 parts of vulcanized rubber, 23 parts of carbon nanotubes, 40 parts of composite conductive filler, 5 parts of ammonium polyphosphate, and 25 parts of propanol , 6 parts of butyl glycidyl ether, 5 parts of zinc stearate, 5 parts of silane coupling agent and 3 parts of bentonite.
[0029] Step 1: Add carbon nanotubes to mixed acid and stir with a magnetic stirrer, then condense and reflux, react at 90°C for 4h, then wash with deionized water until neutral, then vacuum-dry at 95°C for 24h to obtain Modified carbon nanotubes;
[0030] Step 2, put the composite conductive filler, butyl glycidyl ether, zinc stearate and ammonium polyphosphate into a ball mill, grind for 25 minutes at a speed of 1800 rpm, and then filter the mixture with a 260-mesh sieve;
[0031] Step 3, put organic fluorosilicone resin, vulcanized rub...
PUM
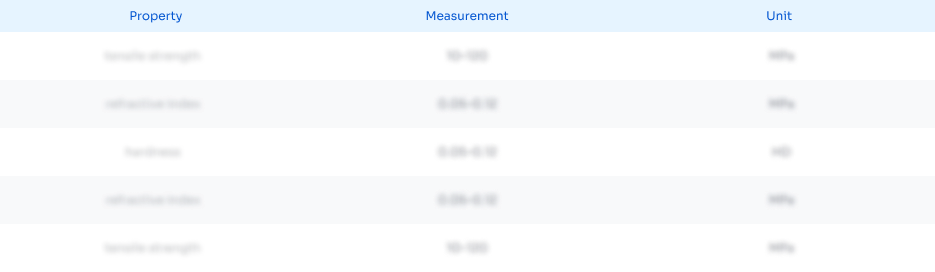
Abstract
Description
Claims
Application Information

- R&D
- Intellectual Property
- Life Sciences
- Materials
- Tech Scout
- Unparalleled Data Quality
- Higher Quality Content
- 60% Fewer Hallucinations
Browse by: Latest US Patents, China's latest patents, Technical Efficacy Thesaurus, Application Domain, Technology Topic, Popular Technical Reports.
© 2025 PatSnap. All rights reserved.Legal|Privacy policy|Modern Slavery Act Transparency Statement|Sitemap|About US| Contact US: help@patsnap.com