Method and system for processing high-iron laterite nickel ore
A technology of lateritic nickel ore and high iron, which is applied in the field of metallurgy, can solve the problems of low yield and low nickel grade, achieve the effects of reducing processing capacity, reducing acid consumption, and solving low nickel grade
- Summary
- Abstract
- Description
- Claims
- Application Information
AI Technical Summary
Problems solved by technology
Method used
Image
Examples
Embodiment 1
[0081] The high-iron laterite nickel ore (containing 1.2wt% of nickel, 0.09wt% of cobalt, and 41.2wt% of iron) is pressed according to the weight ratio of 100 parts by weight of high-iron laterite nickel ore, 10 parts by weight of coal, and 10 parts by weight of limestone. After drying, the pellets are placed in a rotary hearth furnace for reduction at 1200°C for 20 minutes, and the high-temperature flue gas discharged from the rotary hearth furnace is returned to the furnace front system for drying of laterite nickel ore raw materials and pellets. Metallized pellets are subjected to grinding and magnetic separation after water quenching to obtain ferronickel material, and the above-mentioned ferronickel material is evenly sent into a closed tank with stirring, continuously blowing air or oxygen and stirring continuously, and at the same time adding Sodium salts are used as rust catalysts to speed up the rate of selective iron removal, so that the metallic iron in the mine is "...
Embodiment 2
[0083] The high-iron laterite nickel ore (containing 1.1wt% of nickel, 0.1wt% of cobalt, and 32.2wt% of iron) is pressed according to the weight ratio of 100 parts by weight of high-iron laterite nickel ore, 15 parts by weight of coal, and 20 parts by weight of carbide slag. After drying, the pellets are put into the rotary hearth furnace and reduced for 50 minutes at 1300°C. The high-temperature flue gas discharged from the rotary hearth furnace is returned to the furnace front system for drying of laterite nickel ore raw materials and pellets, and is discharged from the discharge port. The metallized pellet products are water-quenched and then subjected to grinding and magnetic separation to obtain ferronickel-containing materials. The above-mentioned ferronickel-containing materials are evenly sent into a closed tank with stirring, continuously blowing air or oxygen and stirring continuously, and at the same time Add potassium salts as rust catalysts to speed up the rate of ...
Embodiment 3
[0085] After the high-iron laterite nickel ore (containing 0.98wt% of nickel, 0.11wt% of cobalt, and iron 34.5wt%) is mixed according to the weight ratio of 100 parts by weight of high-iron laterite nickel ore, 25 parts by weight of coal, and 25 parts by weight of lime and sodium carbonate Pressing balls, the pellets are dried and put into the rotary hearth furnace for reduction for 30 minutes at 1250°C. The high-temperature flue gas discharged from the rotary hearth furnace is returned to the furnace front system for drying of laterite nickel ore raw materials and pellets. The metallized pellet product discharged from the feed port is water-quenched and then subjected to grinding and magnetic separation to obtain ferronickel-containing material. The above-mentioned ferro-nickel-containing magnetic material is evenly sent into a closed tank with stirring, continuously blasting air or oxygen and Stir continuously, and at the same time, add sodium salts as rust catalysts to speed...
PUM
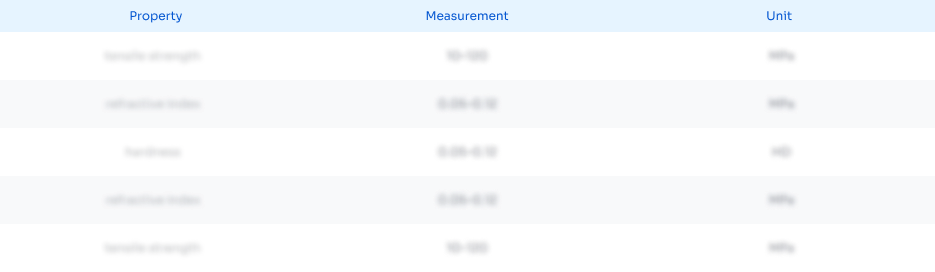
Abstract
Description
Claims
Application Information

- R&D Engineer
- R&D Manager
- IP Professional
- Industry Leading Data Capabilities
- Powerful AI technology
- Patent DNA Extraction
Browse by: Latest US Patents, China's latest patents, Technical Efficacy Thesaurus, Application Domain, Technology Topic, Popular Technical Reports.
© 2024 PatSnap. All rights reserved.Legal|Privacy policy|Modern Slavery Act Transparency Statement|Sitemap|About US| Contact US: help@patsnap.com