Corrosion-resistant magnesium alloy material and preparation method thereof
A magnesium alloy and corrosion-resistant technology, which is applied in the field of corrosion-resistant magnesium alloy materials and its preparation, can solve the problems of low market share of domestic products and achieve high hardness, good oxidation resistance, and easy control of parameters
- Summary
- Abstract
- Description
- Claims
- Application Information
AI Technical Summary
Problems solved by technology
Method used
Examples
Embodiment 1
[0015] A corrosion-resistant magnesium alloy material, made of the following raw materials in parts by weight: 56 parts of magnesium powder, 34 parts of tungsten carbide, 10 parts of zirconium carbide, 45 parts of molybdenum iron powder, 3 parts of analusite powder, 10 parts of vanadium boride, 10 parts of attapulgite clay powder, 1 part of basic nickel carbonate, 2 parts of ditin trioxide, 6 parts of cadmium selenide, and 5 parts of kaolin.
[0016] The steps of the preparation method are as follows: firstly, each raw material is added into a mixer for mixing, then the evenly mixed mixture is added into a press equipment, and pressurized and formed at a pressure of 400-600 MPa, and the pressure is maintained for 10-30 minutes. Then the pressed sample is sintered in the sintering furnace, the preheating temperature is 250-300°C, preheating for 1h, the sintering temperature is 1000-1100°C, the sintering time is 10-30min, and then kept at 250-350°C 10-20min, quenching, and final...
Embodiment 2
[0018] A corrosion-resistant magnesium alloy material, made of the following raw materials in parts by weight: 66 parts of magnesium powder, 44 parts of tungsten carbide, 15 parts of zirconium carbide, 55 parts of molybdenum iron powder, 8 parts of analusite powder, 20 parts of vanadium boride, 10-20 parts of attapulgite clay powder, 6 parts of basic nickel carbonate, 5 parts of ditin trioxide, 7 parts of cadmium selenide, and 8 parts of kaolin.
[0019] The steps of the preparation method are as follows: firstly, each raw material is added into a mixer for mixing, then the evenly mixed mixture is added into a press equipment, and pressurized and formed at a pressure of 400-600 MPa, and the pressure is maintained for 10-30 minutes. Then the pressed sample is sintered in the sintering furnace, the preheating temperature is 250-300°C, preheating for 1h, the sintering temperature is 1000-1100°C, the sintering time is 10-30min, and then kept at 250-350°C 10-20min, quenching, and f...
Embodiment 3
[0021] A corrosion-resistant magnesium alloy material, made of the following raw materials in parts by weight: 59 parts of magnesium powder, 39 parts of tungsten carbide, 13 parts of zirconium carbide, 49 parts of molybdenum iron powder, 6 parts of analusite powder, 15 parts of vanadium boride, 15 parts of attapulgite clay powder, 3 parts of basic nickel carbonate, 4 parts of ditin trioxide, 6 parts of cadmium selenide, and 7 parts of kaolin.
[0022] The steps of the preparation method are as follows: firstly, each raw material is added into a mixer for mixing, then the evenly mixed mixture is added into a press equipment, and pressurized and formed at a pressure of 400-600 MPa, and the pressure is maintained for 10-30 minutes. Then the pressed sample is sintered in the sintering furnace, the preheating temperature is 250-300°C, preheating for 1h, the sintering temperature is 1000-1100°C, the sintering time is 10-30min, and then kept at 250-350°C 10-20min, quenching, and fina...
PUM
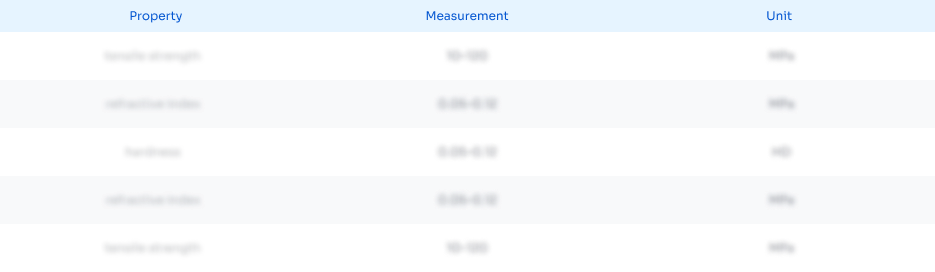
Abstract
Description
Claims
Application Information

- R&D
- Intellectual Property
- Life Sciences
- Materials
- Tech Scout
- Unparalleled Data Quality
- Higher Quality Content
- 60% Fewer Hallucinations
Browse by: Latest US Patents, China's latest patents, Technical Efficacy Thesaurus, Application Domain, Technology Topic, Popular Technical Reports.
© 2025 PatSnap. All rights reserved.Legal|Privacy policy|Modern Slavery Act Transparency Statement|Sitemap|About US| Contact US: help@patsnap.com