Forming mold and method for ultra-fine grain hollow magnesium alloy profile
A technology of forming dies and forming methods, applied in the direction of metal extrusion dies, etc., can solve the problems of poor processing accuracy of thin pipes, reduced mechanical properties of magnesium alloys, unfavorable secondary processing of thin pipes, etc., to simplify the production process, promote Dynamic recrystallization, the effect of eliminating void defects
- Summary
- Abstract
- Description
- Claims
- Application Information
AI Technical Summary
Problems solved by technology
Method used
Image
Examples
Embodiment
[0028] Example: see Figure 1 to Figure 5 , a forming die of an ultrafine-grained hollow magnesium alloy profile, comprising a base 1 , a die casing 2 , a die casing 2 , an extrusion needle 4 , an extrusion shaft 5 and an extrusion pad 6 . The die cover 2 is a tubular structure with a tapered inner hole, and one end of the die cover 2 with a small aperture is fixedly connected to the base 1 . Said die inner cover 3 is arranged in the die outer cover 2, and its outer wall is also conical, and the outer wall of the die inner cover 3 is closely attached to the inner wall of the die outer cover 2; the die inner cover 3 and the die outer cover 2 pass through The tapered structure fits together, so that the die inner sleeve 3 and the die outer sleeve 2 can be combined in a prestressed combination, which can improve the strength of the entire die and prevent the die from being squeezed, so that the overall stability is better and the die is extended. service life; and can significan...
PUM
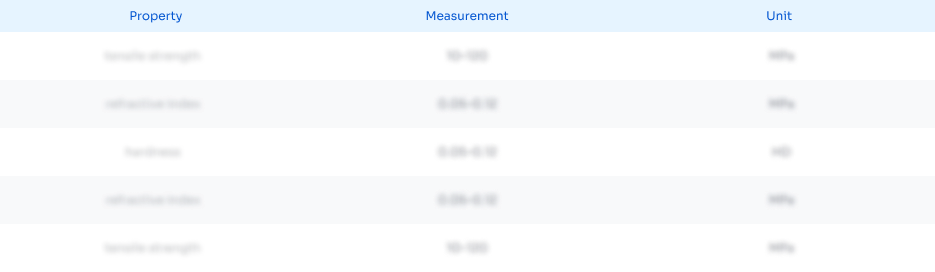
Abstract
Description
Claims
Application Information

- R&D
- Intellectual Property
- Life Sciences
- Materials
- Tech Scout
- Unparalleled Data Quality
- Higher Quality Content
- 60% Fewer Hallucinations
Browse by: Latest US Patents, China's latest patents, Technical Efficacy Thesaurus, Application Domain, Technology Topic, Popular Technical Reports.
© 2025 PatSnap. All rights reserved.Legal|Privacy policy|Modern Slavery Act Transparency Statement|Sitemap|About US| Contact US: help@patsnap.com