Synthesis method of organosilicone modified superfine aluminum hypophosphite
A technology of aluminum hypophosphite and synthesis method, which is applied in the preparation of inorganic flame retardant materials and in the field of inorganic chemistry, can solve the problems of large smoke generation, poor thermal stability, and large hygroscopicity, so as to reduce the dosage and improve the mechanical mechanics Performance, the effect of mild reaction conditions
- Summary
- Abstract
- Description
- Claims
- Application Information
AI Technical Summary
Problems solved by technology
Method used
Examples
Embodiment 1
[0019] Prepare 600g of 30% sodium hypophosphite aqueous solution and 500g of 50% aluminum sulfate aqueous solution. Set the sodium hypophosphite solution as the bottom solution. After the temperature of the bottom solution rises to 85 degrees, add 2g of dispersant and continue to stir. Heating, when the temperature rises to 95 degrees, gradually add aluminum sulfate solution to the sodium hypophosphite solution at a stirring speed of 100r / min and a dripping rate of 20g / min. After the addition is completed, continue to keep the material temperature at 95 degrees and react for 30 minutes. Then, add dropwise an organic silicon solution with a mass fraction of 30% for 0.5h alcoholysis, continue to stir for 0.5h, then cool to room temperature, wash several times and use 5% BaCl 2 Solution inspection, after the filtrate did not produce white precipitate, dried to obtain organic silicon modified ultrafine aluminum hypophosphite product, the yield was 98%, the average particle size was 4...
Embodiment 2
[0021] Prepare 600g of 35% sodium hypophosphite aqueous solution and 500g of 55% aluminum sulfate aqueous solution. Set the sodium hypophosphite solution as the bottom solution. After the temperature of the bottom solution rises to 90 degrees, add 2g of dispersant and continue stirring. Heating, when the temperature rises to 95 degrees, gradually add aluminum sulfate solution to the sodium hypophosphite solution at a stirring speed of 200r / min and a dripping rate of 10g / min. After the addition is completed, continue to keep the material temperature at 95 degrees for 30 minutes. Then add dropwise an organic silicon solution with a mass fraction of 50% alcoholysis for 1 hour, continue to stir for 0.5 hours, then cool to room temperature, wash several times and use 5% BaCl 2 Solution inspection, after the filtrate did not produce white precipitate, dried to obtain the organic silicon modified ultrafine aluminum hypophosphite product, the yield was 99%, and the average particle size ...
Embodiment 3
[0023] Prepare 600g of 40% sodium hypophosphite aqueous solution and 500g of 60% aluminum sulfate aqueous solution. Set the sodium hypophosphite solution as the bottom solution. After the temperature of the bottom solution rises to 90 degrees, add 3g of dispersant and continue to stir. Heating, when the temperature rises to 95 degrees, gradually add aluminum sulfate solution to the sodium hypophosphite solution at a stirring speed of 400r / min and a dripping rate of 5g / min. After the addition is completed, continue to keep the material temperature at 95 degrees and react for 10 minutes. Then add dropwise an organosilicon solution with a mass fraction of 50% for alcoholysis for 0.5 h, continue to stir for 1 h, then cool to room temperature, wash several times and use 5% BaCl 2 Solution inspection, after the filtrate did not produce white precipitate, dried to obtain organosilicon modified ultrafine aluminum hypophosphite product, the yield was 97%, and the average particle size was...
PUM
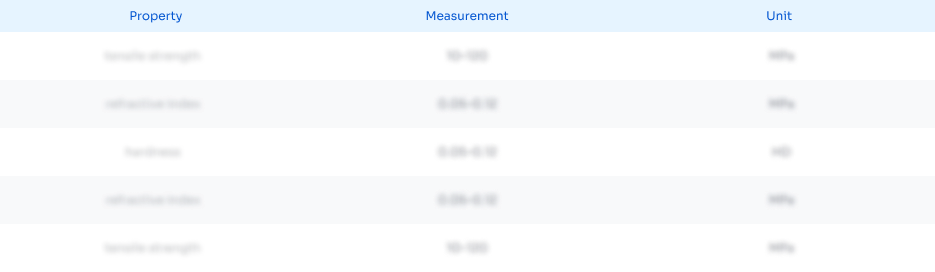
Abstract
Description
Claims
Application Information

- Generate Ideas
- Intellectual Property
- Life Sciences
- Materials
- Tech Scout
- Unparalleled Data Quality
- Higher Quality Content
- 60% Fewer Hallucinations
Browse by: Latest US Patents, China's latest patents, Technical Efficacy Thesaurus, Application Domain, Technology Topic, Popular Technical Reports.
© 2025 PatSnap. All rights reserved.Legal|Privacy policy|Modern Slavery Act Transparency Statement|Sitemap|About US| Contact US: help@patsnap.com